Polymer Service GmbH Merseburg (PSM) and the Fraunhofer Institute for Microstructure of Materials and Systems IMWS want to increase the mechanical performance of composite materials in a joint research project. They are focusing on the surface treatment of carbon reinforcement fibers to better adapt them for use in thermoplastics. Small and medium-sized companies in particular could benefit from these optimized material systems to produce semi-finished products with better performance and less development effort.
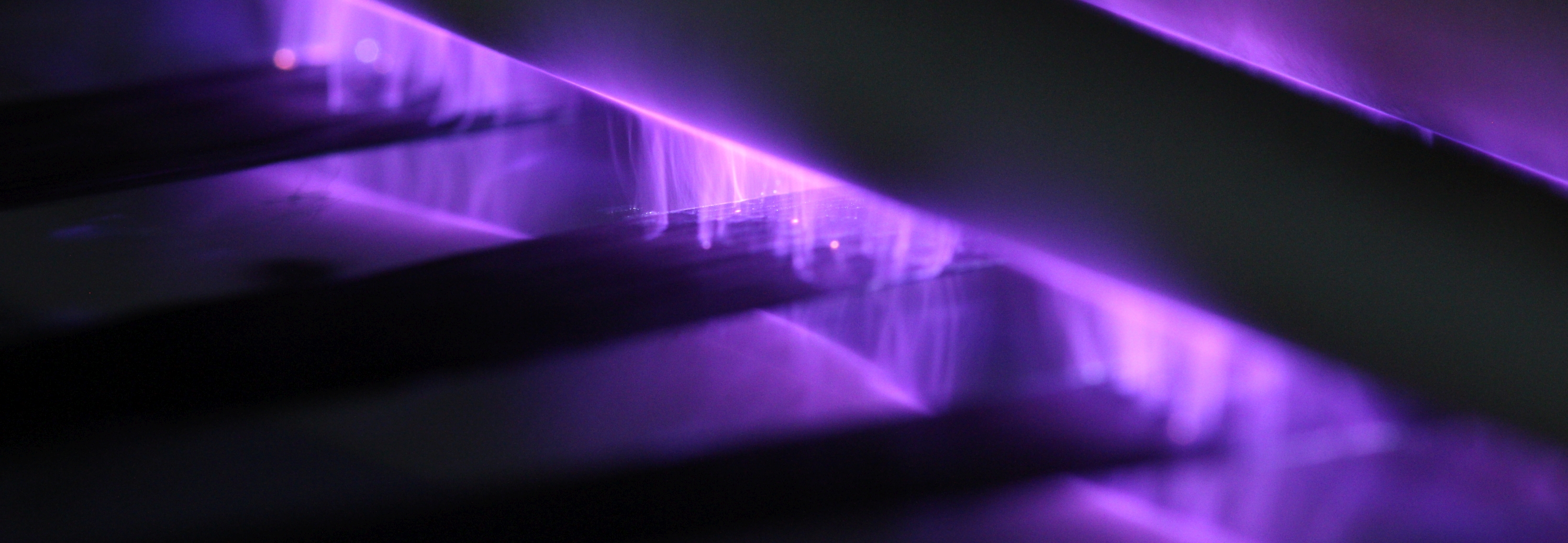

Plastics with unidirectional oriented reinforcement fibers have proven their worth in many areas of lightweight construction. The reinforcing fibers, usually glass or carbon fibers, are introduced into a plastic matrix in such a way that their alignment corresponds optimally to the subsequent load profile in the component. This approach is usually implemented with thermoset systems, i.e. a manufacturing method in which the plastic components, once produced, cannot be deformed later.
"This implies several disadvantages. The manufacturing process is costly and time-consuming. Furthermore, thermoset material systems can not be recycled. We are therefore focusing on thermoplastics and want to improve the possible applications of carbon fibers in this area in particular," says Nico Teuscher, who heads the project at the Fraunhofer IMWS, which runs until April 2022 as part of the Chemistry and Biosystems Engineering Performance and Transfer Center. Thermoplastic-based material systems with unidirectional reinforcing fibers, so-called organosheets or UD tapes, are already available on the market and offer ideal conditions for use in series applications for large quantities because they can be processed easily and quickly. So far, however, they have been available mainly with glass fibers and thus do not fully exploit their potential.
"UD tapes with carbon fibers have even better mechanical properties, for example in terms of tensile strength. They are therefore very appealing, especially for use in structural components that can withstand high loads. So far, however, carbon fibers have been designed primarily for use in thermoset systems. In the project, we want to optimize them for thermoplastics. Then the strengths of UD tapes could be ideally combined with the strengths of carbon fibers," says Teuscher.
This requires, for example, adaptation of the fiber surfaces and fiber impregnation so that the reinforcing elements embed well and uniformly in a thermoplastic matrix and bond optimally to it. The aim is to find a solution that allows individual surface treatment of the fiber, which is tailored to the matrix material in question and can be integrated directly (inline) into the UD tape production process. Small and medium-sized companies in particular, such as automotive suppliers, could benefit from this, because standard carbon fibers can then be used for their applications instead of having to develop their own sizing of the fibers that is precisely tailored to the respective thermoplastic matrix at great expense.
The project partners want to modify the surface of standard carbon fibers available on the market by means of atmospheric plasma treatment in such a way that the fiber-matrix coupling is improved when used in thermoplastics and the impregnation behavior of the fibers is optimized. The focus is both on the effects of the novel approach of atmospheric plasma discharges under ambient air on the surface energy, morphology, surface chemistry and interfacial properties of carbon fibers, and on the selection of additional substances (precursors, inert gases) that may be helpful for the process. The result of the project should be a demonstration of inline plasma modification in the process of melt impregnation of the fibers.
In addition to the detailed evaluation of the mechanical properties and morphology of the resulting tapes, new evaluation methods for fiber-matrix adhesion are also being developed for this purpose. The project partners are also looking at whether the achievable performance increases also justify the additional effort in economic terms, for example having in mind material costs or the effects on process speed. The possibility of testing in industry-compatible plants at the PAZ pilot plant center offers ideal conditions for this.
"If we are successful, unidirectionally reinforced thermoplastics can be used for even more fields of application in lightweight construction. They have outstanding mechanical properties and can thus replace, for example, significantly heavier metal parts or even thermoset solutions in the area of highly stressable structural systems. That would be a major contribution to sustainability," says Teuscher.