Fewer process failures and build errors due to semi-automated quality assurance for 3-D printed components
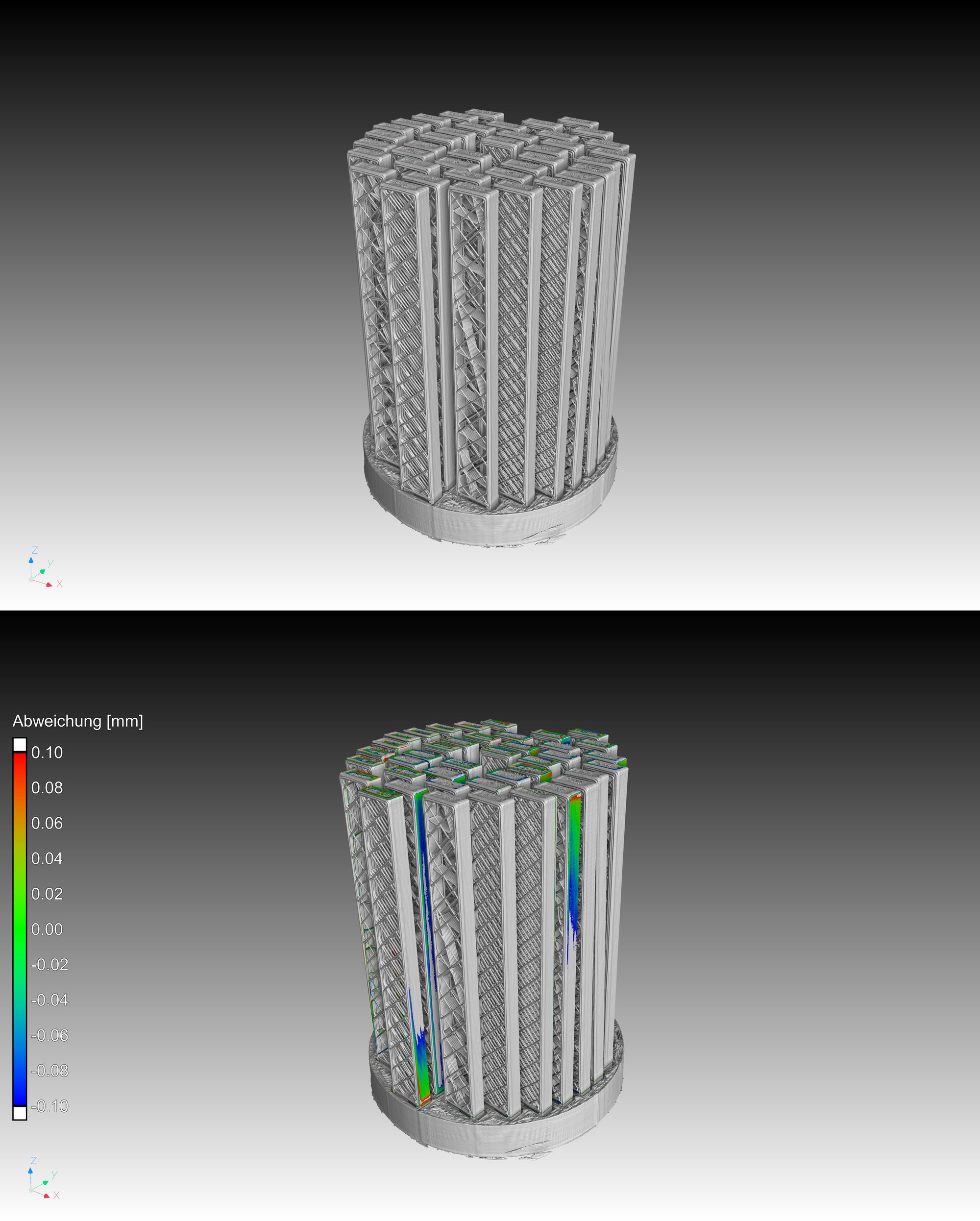

The digitization of production processes enables enormous increases in efficiency in industrial production. Additive manufacturing is a key technology used in this process. It makes it possible to produce components efficiently and sustainably, from individualized single components to small batches of up to approximately 1000 units. From design to manufacturing, the work process is digital.
However, for this process to function smoothly in the sense of an industry 4.0, individual steps of the workflow must be adapted. The automated feeding of operating and raw materials, component tracking, component handling and automated, even random, inspection, however, currently present challenges that still have to be solved. In particular, the requirements for automatic quality assurance play a role that should not be underestimated.
The joint project of Studio.201 Software GmbH and Fraunhofer IMWS focuses on semi-automated quality assurance for 3D printed components. The main idea of the approach is to automatically inspect additively manufactured components in parallel so as to reduce component distortions and detect defects. For this purpose, process and geometrical data (target data) is to be linked with previously determined measurement data from computed tomography (actual data) on large samples (<100). The data obtained through this process in turn creates a database for the machine learning required in subsequent processes. Supplemented by automated component tracking, this creates the possibility for establishing an integrated process control in the future. "Thus, it is possible to automatically correlate data from design and preliminary development, accompanied by process data, to the measurement data of the final component, in order to implement adjustments to the technology, material selection or in steps for post-processing, improving reproducibility," says Andreas Krombholz, head of the project at Fraunhofer IMWS.
Due to the increased number of variations in additive than in conventional manufacturing, the variations are tested within the framework of an automated evaluation using Massive Parallel Testing (MPT) in the present method. Based on the geometric design of a component, many constructive versions are automatically created, combined with the variants of the manufacturing process and different materials, and additively manufactured. For this purpose, a tracking and handling system is being developed to prepare the printed components for structural examination using computer tomography and then to examine them microstructurally. This is accompanied and documented by a data management system. Finally, a quantitative evaluation and a statement in form of a traffic light system are available for each manufactured variant. This enables the user to identify optimal component-material-process variants and then manufacture these optimized components in small batches.