Components made from plastic for lightweight construction applications are increasing in importance. Many of them – such as pipes, car interiors or packaging – are produced using an injection moulding process. Polymer is melted in granulate form in an injection moulding machine and pressed into a mould under high pressure. When the material hardens, crystals are produced, which are crucial to the properties of the component. Until now, it has not been possible to control crystallisation during the injection moulding process so much to achieve very light polymer-based components with optimally adapted mechanical properties such as strength and flexibility.
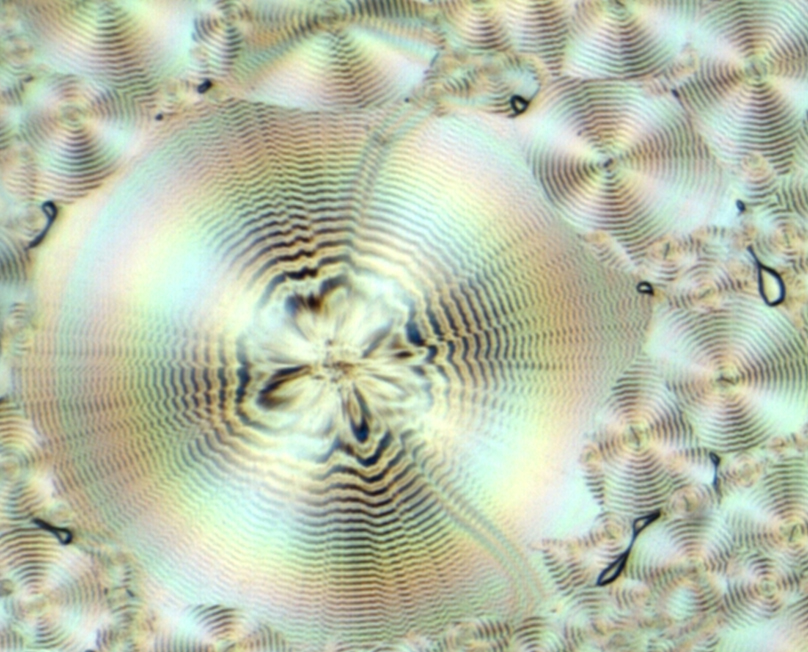

Researchers from the Fraunhofer Institute for Microstructure of Materials and Systems IMWS Halle (Saale), the Martin Luther University of Halle-Wittenberg and the Otto von Guericke University Magdeburg are now developing a fundamental concept and numerical simulation methods in a joint project, which will in future allow crystallisation to specifically adapted or optimised during the manufacture of injection moulded parts made from plastic.
Within the scope of the expertise alliance, questions from the areas of polymer processing will be brought together with polymer-based material design, new knowledge on polymer crystallisation in injection moulding processes will be gained and implemented in practical application models. In order to reach this goal, the correlations between the mechanical properties of the injection moulded component, the inner structure of the spatially inhomogeneous partially crystalline component and the applied process parameters must be understood. The joint project, which runs until 30th September 2019, specifically concentrates on the influence of the temperature regime on the mechanical properties when manufacturing injection moulded components.
Numerical simulation methods that allow a calculation of the mechanical properties of structurally inhomogeneous components to be linked with the results of thermodynamic examinations. This allows forecasts to be made regarding the fast crystallisation processes during the injection moulding process. The researchers want to develop a sensor system for the very first time, which records the cooling process and therefore the crystallisation process of the polymer inline – there directly during the manufacturing process.
»We are collating data both in the laboratory and also during simulation and are carefully examining the component geometry. At the end, we can predict how crystallisation in the components works in detail. This allows us to produce injected moulded components with higher quality – meaning that we achieve higher material efficiency and improve performance«, says Prof. Mario Beiner, project leader at Fraunhofer IMWS.
In order to understand how the material in the injection moulding form cools and crystallises, experiments on the processing parameters of the polymer in the laboratory as well as the manufacture of model components and inline measurements in a mini injection moulding machine are required. The mechanical characteristic values for model components with varying crystallisation states are determined in experiments and compared with the results of numerical simulations for inhomogeneous components.
Different process parameters are varied for the manufacture of model components and a specially developed, sensor controlled injection moulding form for a mini injection moulding machine is used. This method allows the mechanical properties and the inhomogeneous partially crystalline structure of the model component to be specifically influenced. With the aid of subsequent x-ray and scanning electron microscopic examinations, the influence of the temperature program on the partially crystalline state of the components is analysed in laboratory experiments.
The simulation models to be developed should lead to a demonstrator and act as a preliminary product to prepare for and initiate further associated research projects with the involvement of industry partners – especially from Saxony-Anhalt. After all, the project partners are endeavouring to establish a research alliance, centered around Saxony-Anhalt, with international recognition and the involvement of industry. »We want to specifically develop the interface between fundamental research and applied research in our joint project involving three research institutes and four work groups. We are hoping for a unique international position with high economic potential«, says Prof. Beiner summarising the project.