Filter stuffing unit with integrated glue application for cellulose fibers
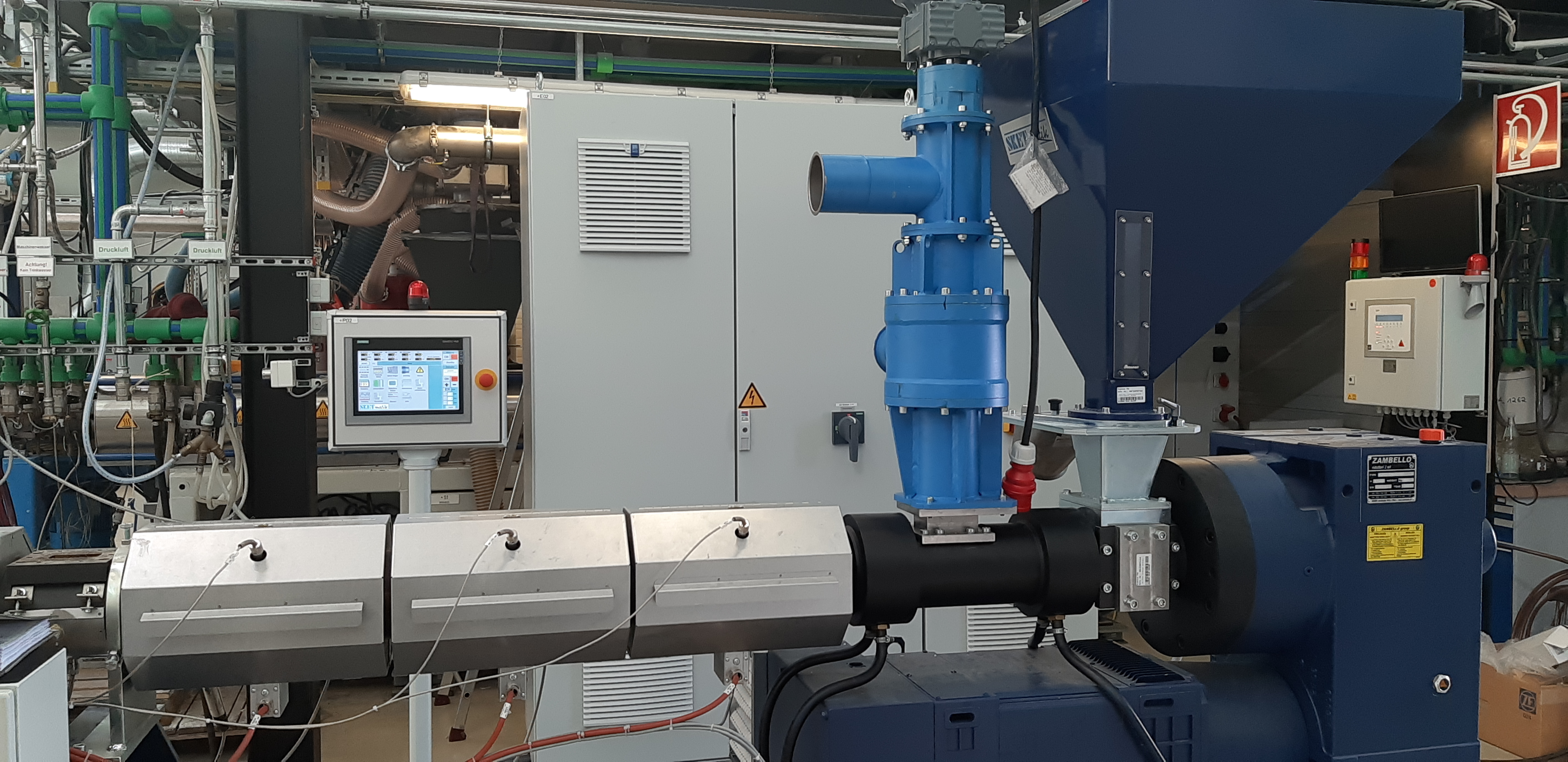
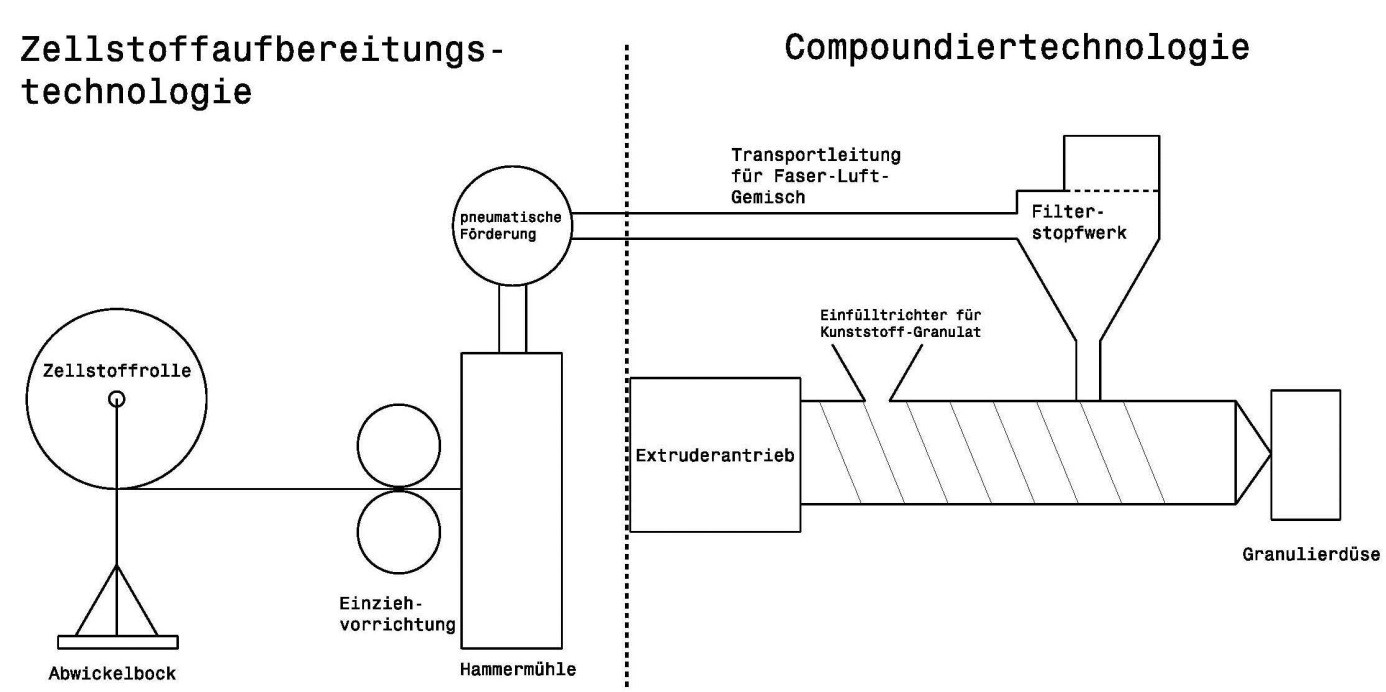

Plastics reinforced with cellulose fibers can serve as an ecological alternative to materials reinforced with glass fibers. For high quality applications, the fibers have to be bonded with the plastic matrix. To this end, Kurt Seume Spezialmaschinenbau GmbH and the Fraunhofer Institute for Microstructure of Materials and Systems IMWS are developing a filter stuffing unit with the integrated application of glue to the fibers, optimizing the adhesion between the cellulose fibers and plastic.
Thermoplastic materials such as polypropylene (PP), polyethylene (PE), and others are reinforced with fibers to obtain application-specific properties. Such fiber compounds are used in automobile components such as instrument panels or side paneling, in the housings of electrical equipment, for garden furniture, shipping containers, and other plastic parts and fields of application. The components are very robust and also lightweight. Glass fiber reinforced compounds account for the largest proportion by far.
Meanwhile the demand for natural fibers as reinforcing materials is increasing. Aside from the lower specific compound weight and reduced tool wear during processing of the compounds, this is owed to the benefits of natural fibers in the life cycle assessment. The CO2 footprint of natural fibers is much smaller compared to glass and mineral fibers. In cellulose production, the non-process-related emissions from energy generation originate mainly from renewable raw materials and therefore do not impact the CO2 cycle (the process-related CO2 emissions are negligible).
In order for the fiber compound to exhibit favorable properties, the fibers have to be bonded with the plastic matrix in which they are embedded. Applying a fiber and plastic-specific size to the fiber surface has proven itself here. While the size can be applied to glass fibers in a size bath immediately after the fiber filament comes out of the melting vat, and therefore without additional effort, the size application for cellulose fibers requires additional process steps that make the fiber more expensive, which is why it is not used commercially.
Kurt Seume Spezialmaschinenbau GmbH and Fraunhofer IMWS want to change this in their new joint project. They are building on experience gained in a previous project. “We developed a system for the efficient inline processing of cellulose fibers for compounding in cooperation with other partners. It makes the continuous introduction of the cellulose fibers into the polymer melt possible in the first place, thereby enabling the production of cellulose-PP compounds. However, we noted that the properties of the compounds were not adequate for demanding technical applications because the fiber size is currently lacking,” says Dr. Michael Busch, who heads the project at Fraunhofer IMWS.
The centerpiece of the existing inline technology is a filter stuffing unit that filters individual fibers from the cellulose with an air stream and transports them into the compounder-extruder, where they are integrated into the plastic melt. In the project that has now begun, the fiber size is to be additionally integrated into the current process. The project partners intend to apply glue to the cellulose fibers. This contributes to hydrophobizing, which means the cellulose absorbs less water and therefore integrates better with the hydrophobic plastic matrix.
“Glue is to be applied to the fibers in the filter stuffing unit, enabling consistent size application to individual cellulose fibers,” is how Busch describes the approach. While this component is being developed by Seume GmbH, Fraunhofer IMWS is handling the material science investigations regarding the influence of glue application to fibers on the properties of cellulose-PP compounds. This includes, for example, the selection of the sizes to be applied to the fibers and their influence on the processing behavior, and ultimately on the mechanical properties of the compound. Reference values are first being determined for cellulose-PP compounds with no glue application to the cellulose fibers. Suitable formulations for sizes will then be identified, followed by compounding tests with the application of glue to the cellulose fibers using a pilot plant at the Fraunhofer Pilot Plant Center for Polymer Synthesis and Processing PAZ.
“Our goal is to produce high quality cellulose fiber compounds with the application of glue to the cellulose fibers in a highly efficient process. If we succeed, we will open up new fields of application for the use of cellulose fibers as a renewable raw material and thus for new plastic products reinforced with natural fibers. These will be comparable to short glass fiber reinforced plastics in price and performance, but considerably surpass them in the life cycle assessment,” says Busch.