High-quality and complex composite materials for lightweight construction already play an important role for the aviation industry. Fraunhofer IMWS and the aviation supplier P-D Aircraft Interior want to make these materials even more robust by using glass fibres. This would open up further potential for saving weight – thereby reducing fuel consumption and the strain on the environment.
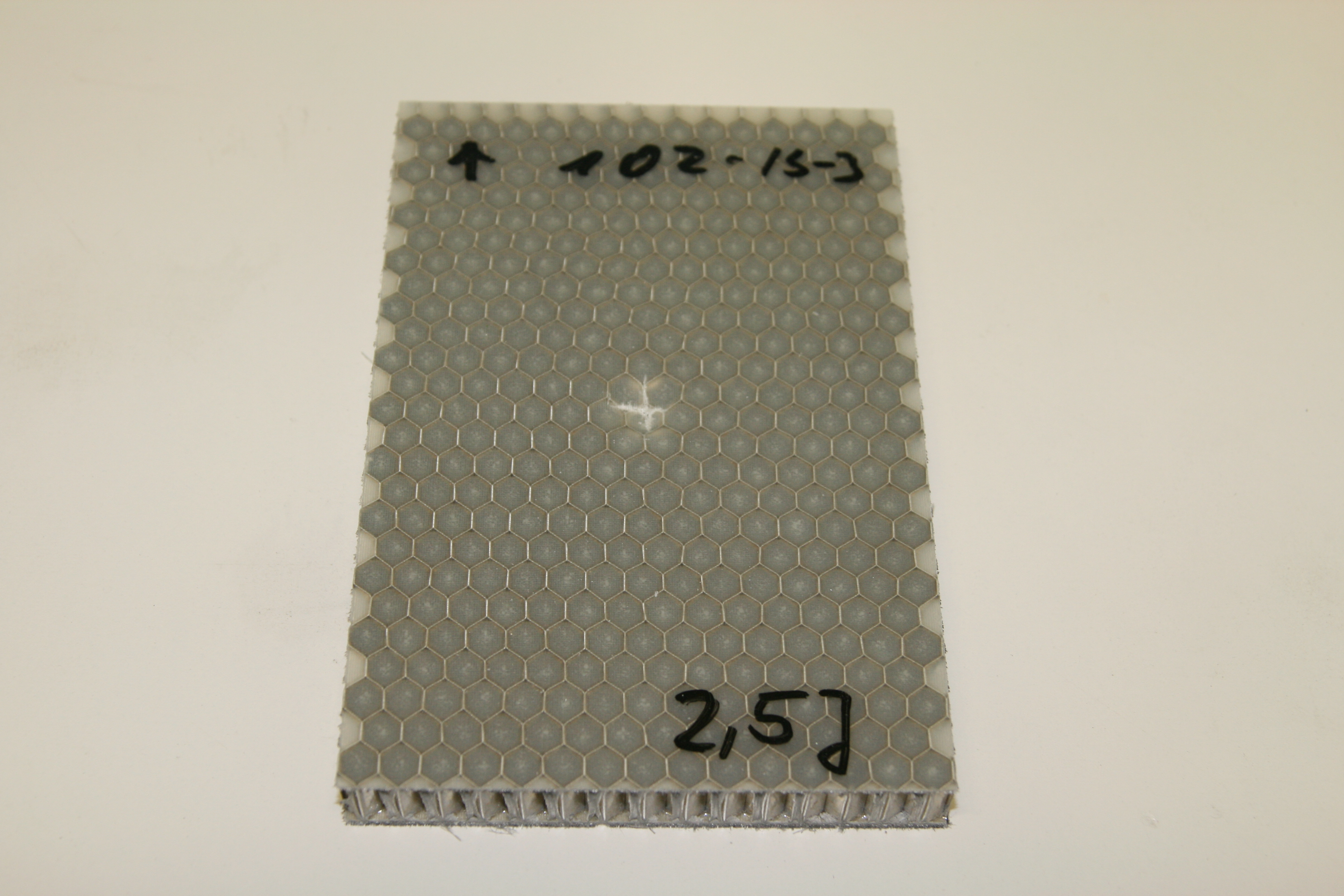

A sandwich in the airplane? Most probably think of the onboard catering and a little snack on a long journey. However, sandwich structures are crucial somewhere very different in the airplane: Components made in this way make their contribution towards reducing the weight of the plane and its consumption of fuel.
Sandwich structures are made of a light core, which can be made of polymer foam or a paper honeycomb structure for example, and solid top layers – these top layers are like the sandwich bread. They are made from modern fibre composite materials and, in combination with the light core, make a sandwich structure with high bending and denting resistance with very low weight. Sandwich structures are therefore the first choice wherever light materials for planar structures are required, which can withstand high loads.
In aircraft construction, sandwich structures are used in cladding parts, functional surfaces on the wings (rudder) as well as inside as flooring panels and wall or ceiling cladding, for example. The components are exceedingly sturdy with their very thin top layers and cores made of light paper honeycomb but are not very resistance to sudden loads (impact). Even a very small and hardly visible damage, such as a bird strike or a fallen object on the flooring can lead to the top layer detaching from the core (delamination) reducing the remaining load capacity of the component considerably.
In order to prevent this, the sandwich structures are often reinforced locally. Metallic inserts and core materials (such as aluminium foam) are frequently added to the sandwich core and the top layers also provided with additional metal layers such as aluminium or steel sheets. This does increase the impact resistance, but it makes the component heavier and thereby counteracts the actual aim of saving weight.
Together with P-D Aircraft Interior GmbH from Bitterfeld, Fraunhofer IMWS wants to create a solution: In the joint project »ImPreg«, which is running until October 2017, the project partners want to develop a top layer material consisting of fibre-reinforced laminates. It should provide the protection against sudden loads currently provided by the metallic materials, but simultaneously retain the weight advantage of the sandwich structures.
The starting material for these high-performance top layers should be glass fibre prepregs. Such prepregs are an important element in the production process. They are a preliminary form of the subsequent component and already contain reinforcement fibres and a matrix material, which encloses the fibres, thereby supporting and fixing. These components harden under the influence of temperature and pressure during processing, so that the component achieves the required properties. P-D Aircraft Interior and Fraunhofer IMWS have already developed suitable prepregs for aircraft construction in a previous project – the method was awarded the Hugo-Junkers-Prize in the specialist category »Resource efficiency« in 2014. »In order to make these prepregs suitable for use in components that are subject to impact loads, they have to be modified. These new materials also have to meet the safety standards of the aviation industry. We will therefore be developing appropriate testing methods to reliably prove that the fibreglass-reinforced top layers offer the necessary quality«, says Ralf Schlimper, who looks after the project at Fraunhofer IMWS.
The plan is to insert high module glass fibres and functional intermediate layers, such as aluminium foil, into the prepregs. The corresponding technological implement (prepreg, laminate and sandwich manufacturing) is also part of the project. Whilst P-D Aircraft Interior GmbH is pushing prepreg technology forwards, Fraunhofer IMWS is covering the testing and evaluation concepts.