Developers and users of lightweight construction solutions are increasingly relying on plastic-based composite materials. Some typical examples are fiber-reinforced plastics, which are used in aircraft construction and the automotive industry to reduce weight and fuel consumption, for example, and ultimately to protect the environment. In a joint research project, the Fraunhofer Institute for Microstructure of Materials and Systems IMWS and Deutsche Basaltfaser DBF GmbH are working together to develop innovative thermoplastic composites with reinforcement fibers made from basalt.
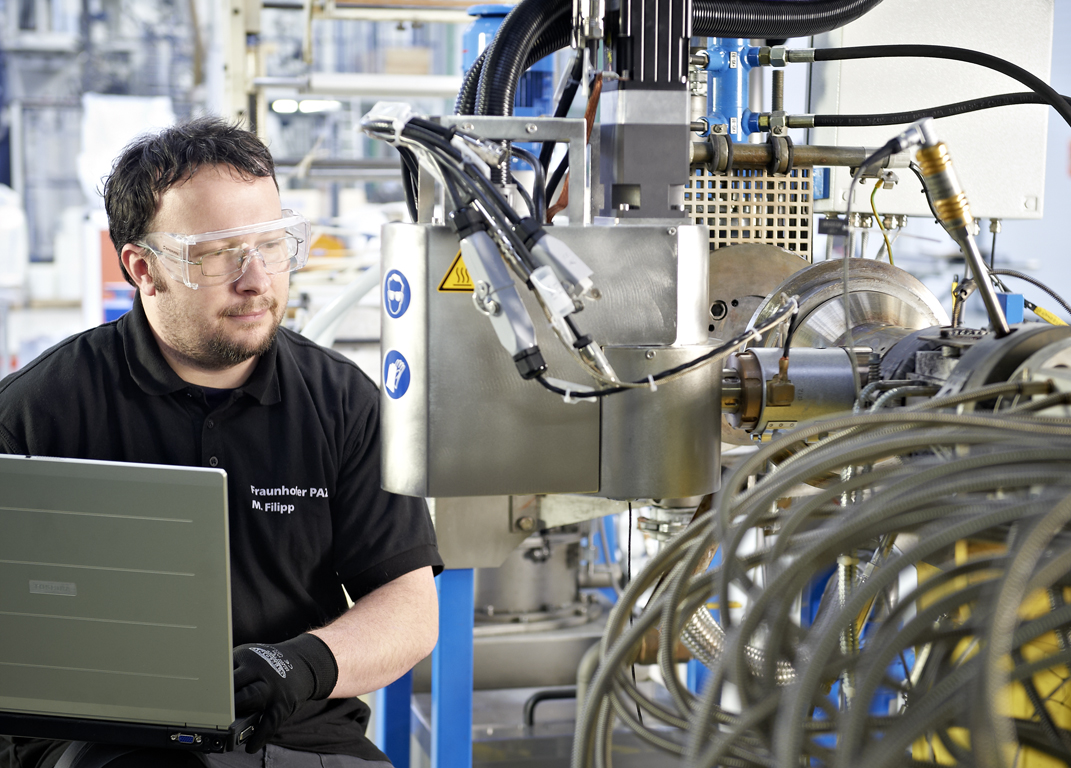

Basalt is a natural volcanic mineral rock. It is used especially in the construction and electrical industry for heat shields, heat insulation and fire protection components in cable insulators and ground connections. Because of basalt’s high thermal resistance and good insulating and mechanical properties, its low water absorption and strong resistance to corrosive liquids, thermosetting basalt-fiber composite materials have already been used in the past.
However, there have not yet been any relevant applications using basalt-fiber reinforcement in the area of thermoplastic composites (TPCs), which are especially interesting for automotive applications. “We want to take advantage of basalt fiber’s very good characteristic profiles compared to glass fiber and its good availability compared to carbon fibers, and we see great potential for economical lightweight construction applications with continuous basalt fibers in the mobility field,” says Ivonne Jahn, group leader for the Thermoplastic Semi-Finished Fiber Composites department at the Fraunhofer IMWS.
To make the basalt fibers usable as reinforcement fibers for thermoplastic composites, however, a few other issues must first be solved. There is currently no satisfactory way to bind basalt fibers to the thermoplastic matrix systems. In addition, the fibers are difficult to handle during manufacturing and further processing.
The joint research project “Innovative basalt-fiber-reinforced thermoplastics for automotive applications” by the Fraunhofer IMWS and Deutsche Basaltfaser GmbH hopes to find solutions for this. The research project, which will run through March 31, 2019, particularly focuses on optimizing the fiber-matrix interface and fiber handling.
Based on scientific studies of short-fiber-reinforced basalt-fiber TPC systems, the first part of the research project will study the influence of various material and technology-related parameters: fiber geometry, fiber pre-treatment, the addition of modifiers, and optimizing the compounding process. It will identify the influence parameters that are significant for the successful and efficient development of basalt-fiber-reinforced thermoplastics as compounds with optimized mechanical properties, for use as an injection molding material in automobile manufacturing.
The second part of the research project will apply the resulting findings to continuous-fiber-reinforced semi-finished TPC products made with basalt fiber. Based on the identified material and process-related influence parameters, the material scientists hope to manufacture UD tapes with basalt fibers (thermoplastic films unidirectionally reinforced with continuous fibers) and use them to make corresponding laminates.
Finally, during the third phase of the project, they will use a demonstrator to validate and create component applications for the newly developed material and process concepts. The technology of hybrid injection molding will be used here, combining continuous fiber-reinforced laminate inlays with short or long fiber-reinforced injection-molded material. “Our research project is an outstanding way to combine high-performance fibers made from natural basalt stone with efficient thermoplastic processing technologies. Our ultimate goal is to develop industry-oriented processing technologies with innovative thermoplastic lightweight construction materials for automobile construction,” summarizes Ivonne Jahn.