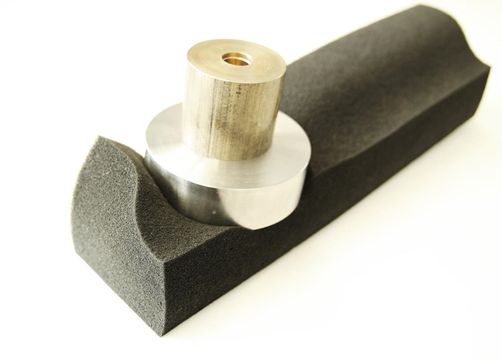
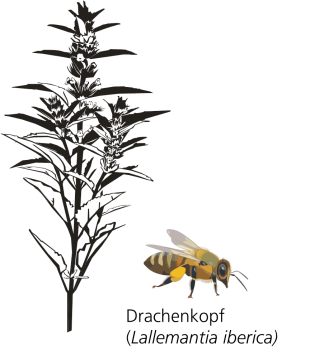

The Iberian dragon's head (Lallemantia iberica) has two important properties that make it an object worthy of study at the Fraunhofer Institute for Microstructure of Materials and Systems IMWS: Firstly, its oil contains a lot of linolenic acid, which makes it a good starting point for organic plastics. Secondly, it is an undemanding plant that can be cultivated in our latitudes and whose flowers can serve as a source of food for bees, for example. If its cultivation is expanded for use in the production of biopolymers, then it can also contribute to counteracting monocultures and the effects of industrial agriculture on the habitats of insects.
Together with the Altermann GmbH and the Fraunhofer Center for Chemical-Biotechnological Processes CBP, the researchers in Halle want to develop a foam within three years that possesses a much better ecobalance than conventional polymer foams made of polystyrene or polyurethane, for example, whose production requires lots of energy and oil. The materials of choice in the research project now being started are renewable: various vegetable oils with a high percentage of polyunsaturated linolenic acid. They are first epoxidized, after which their suitability as a material for a new type of foam is assessed. A prototype should be available at the end of the project that verifies the performance of the material.
Two aspects are especially important to the project partners. First, the sustainability of the materials used should be evaluated as holistically as possible. “To be able to really compare the materials used in this regard, an overall assessment starting with the production of the materials and their use in manufacturing to their use at the end of their life cycle is imperative. This Life Cycle Assessment (LCA) will be conducted in the framework of the project”, said Nicole Eversmann, who supervises these activities at the Fraunhofer IMWS. For this reason, biogenic hardeners and additives will also be used in the foam to be developed. In total, 80-100 percent of the new material should consist of renewable raw materials. The foam should exhibit good storage properties, low thermal conductivity, and higher fire resistance, which would then open up its use in a variety of potential applications.
Secondly, the project team is aiming to develop an adaptive and functionalized foam. Such a foam with an ecological material recipe should have an adjustable curing time or exhibit an especially high heat capacity through functionalization, for example. An adaptive foam offers major advantages in applications because it incorporates itself into various environments. In addition, its transport is significantly more efficient: The foam can be compressed before it is loaded on a truck, for example, and will then re-expand once it arrives at its destination. In this manner, a significantly larger quantity of foam can be transported per load, which in turn reduces emissions and costs.
The research includes the quantitative and qualitative assessment of the new material, and the project partners also want be able to create a digital representation in the framework of the Material Data Space (MDS) by determining the material and process parameters. They also have an eye on the manufacturing processes required: “We will make sure that it is possible to produce the foam using conventional technologies or by making minor adjustments to such technologies. Companies that want to offer their customers a sustainable product could then produce the new material quickly using their existing systems”, said Eversmann.
A welcome side effect is that the use of dragon’s head oil to produce the foam could also create safe havens for insects. The plant offers another advantage in ecological terms. It can be grown in the region where it is used, which means no more long transport routes. “If I really want to reduce the carbon footprint of a product, then the transport route also needs to be taken into account”, said Eversmann.