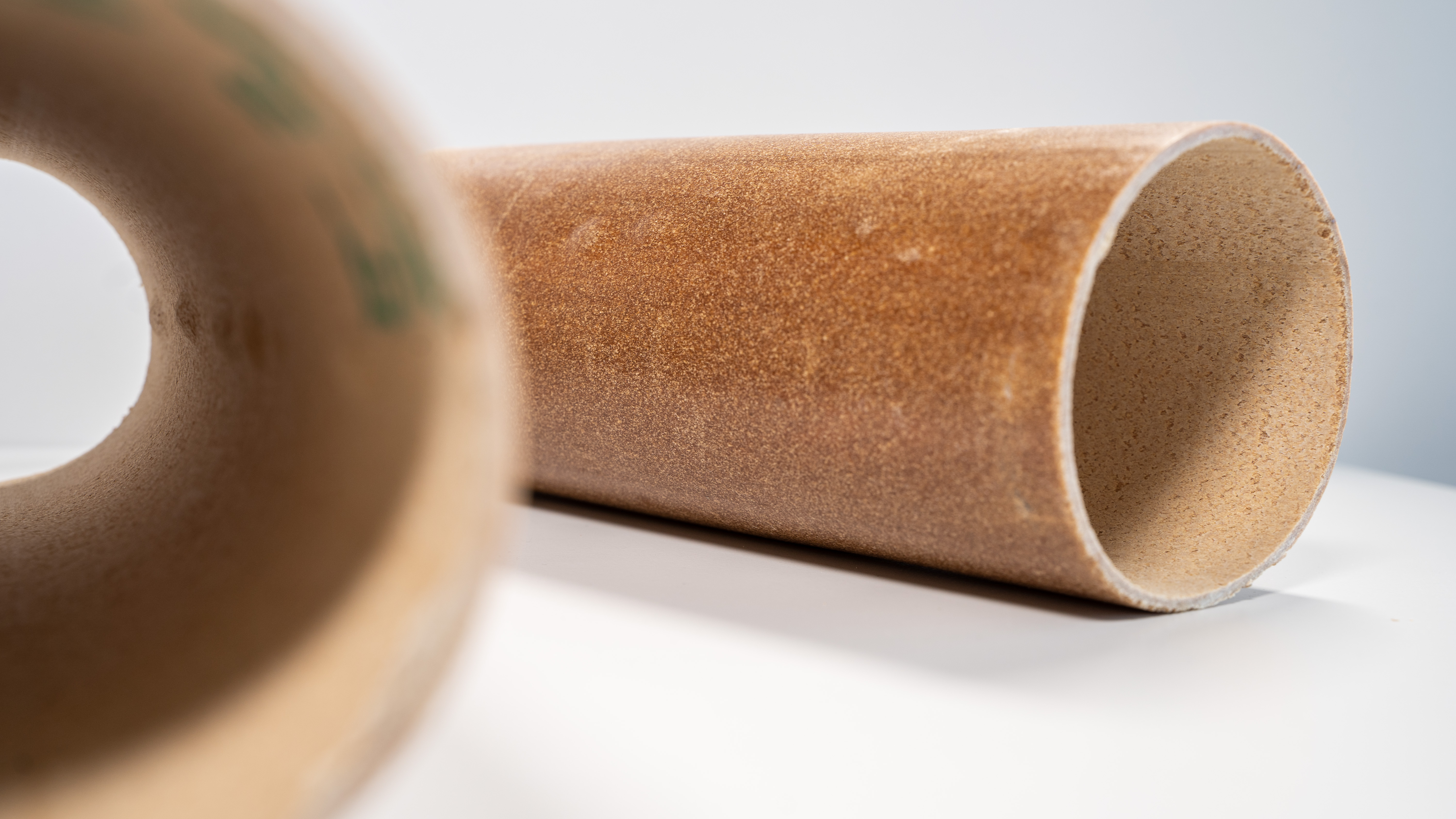
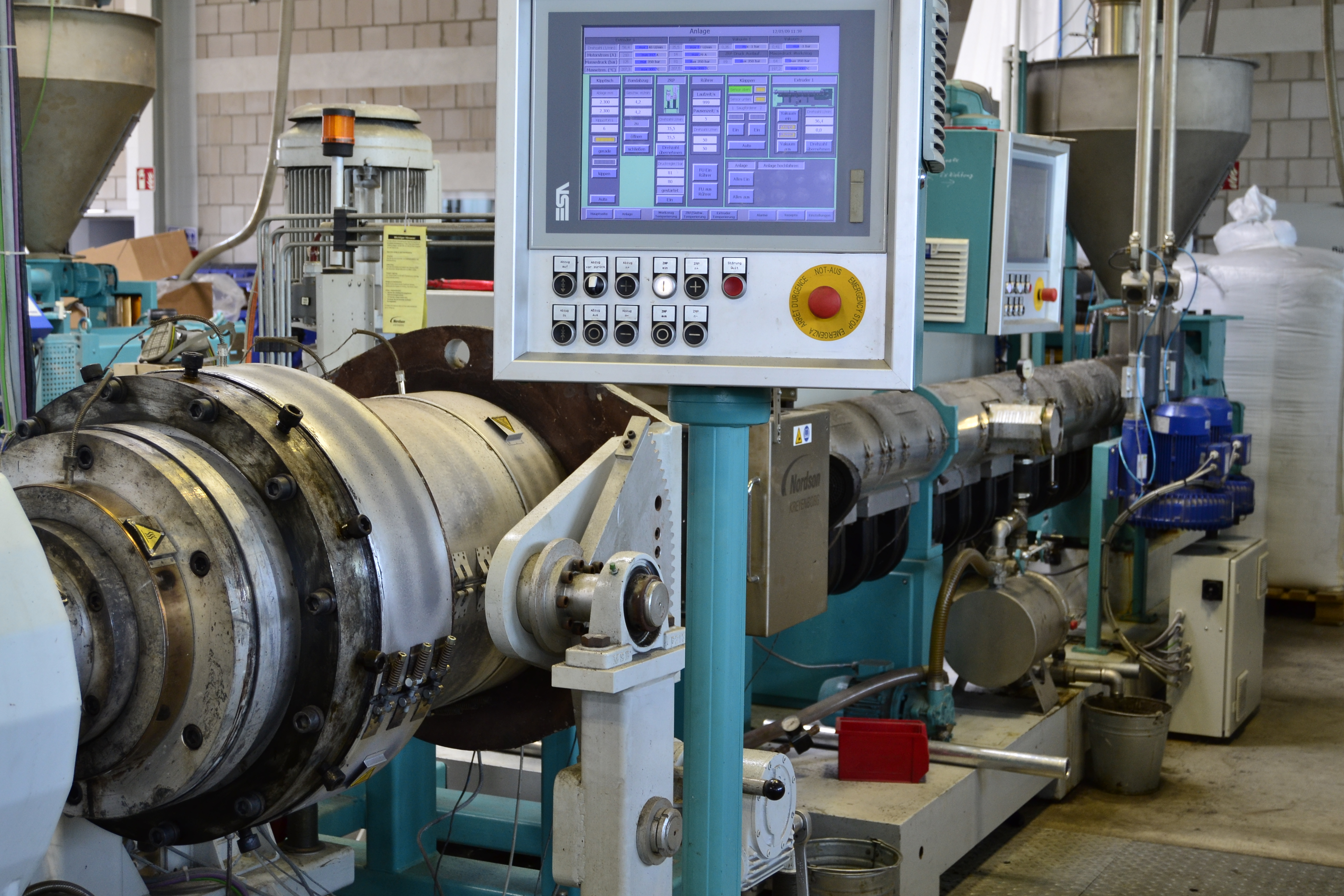

Wood flour and starch are readily available, natural raw materials. In a joint research project, Thermoplast GmbH and the Fraunhofer Institute for Microstructure of Materials and Systems IMWS tested the suitability of these biomaterials for the production of environmentally friendly wood flour-starch compounds and their processing into profiles. As a result of the project, the potential of this biomaterial could be demonstrated.
Winding cores are in demand wherever materials are wound into rolls, such as films or carpets. The cores form the core of the roll and are made either of paper or plastic, depending on the mechanical requirements. They must be lightweight and very precisely formed. "Even the smallest deviations in size or unevenness on the surface can cause damage to the sensitive material being wound," explains Markus Weissgärber of Thermoplast GmbH, which manufactures such cores.
In a research project that has been running for two years, the company has now joined forces with the Fraunhofer IMWS to investigate whether such components can be made from renewable raw materials instead of polyethylene, as was previously the case, to a comparable quality and at competitive prices. The advantages are obvious: winding cores are disposable products, and instead of petroleum, materials could be used that are easy to process and biodegradable. Wood flour is already used significantly as a material in WPC decking boards, and starch is used in paper production and many other industries. "The biomaterials have a significantly improved CO2 footprint, which we can now quantify through the project. In addition, the recyclability of the wood-starch compound, which was not foreseeable at the beginning of the project, has proven to be another advantage," Weissgärber said.
The project consisted of a materials engineering part at the Fraunhofer IMWS for the development of thermoplastically processable wood flour-starch compounds with high wood flour contents and a process engineering part at Thermoplast GmbH for the processing of the wood flour-starch compounds. From the starting materials starch, wood flour and additives, wood flour-starch granulates were developed at the Fraunhofer IMWS, which were further processed into profiles at Thermoplast GmbH.
At the beginning of the project, the insufficiently known properties of starch when used for technical applications as well as the intended high proportion of wood flour in the compounds raised questions regarding material behavior, processability and service properties. The first task was to find suitable starting components. For their thermoplastic processing, the native starch was prepared into thermoplastic starch in a first process step. This was done using a twin-screw extruder with the addition of plasticizers at elevated temperature and under high shear. Glycerine, a readily available and inexpensive by-product of biodiesel production, was used as the plasticizer. In addition to glycerin, water and other sugar alcohols are also suitable plasticizers. Both the formulation (proportions of starch, water, plasticizer, additives) and the processing conditions (screw configuration, temperature, speed, degassing) were systematically investigated with regard to their influence on properties such as viscosity, moisture content before and after processing, water resistance of the compounds, elongation at break and strength.
Different proportions of wood flour were incorporated into the thermoplastic starch. In the project, the aim was to achieve the highest possible proportion of wood flour. It was shown that wood contents in excess of 40% are possible if, at the same time, higher proportions of plasticizers are used in the thermoplastic starch. A particular challenge was the efficient production of the thermoplastic starch and the incorporation of wood flour in a single process step directly from the starting components to the finished granules. "This makes production significantly more energy- and cost-efficient," says Busch. As an important result of the project, it was shown that one-step processing is possible and, in addition to cost advantages, even enables property advantages.
The project objective of developing biodegradable, extruded profiles from wood flour starch compounds with application potential was met. The key innovation was the provision of fully bio-based and biodegradable compounds that could be processed into technical products using the profile extrusion processing method suitable for large-scale production.
As a result of the project, technologies are available for the efficient production of the compounds and for processing the compounds into profiles, as well as comprehensive technological and materials science knowledge. For the development of industrial products following the project, a scientifically sound understanding of the complex formulation influence on the processing behavior and the achievable product properties was gained.
Through the combination of an experienced mechanical engineering company and a research institution active in the field, new experience in cooperation was gained on both sides and the foundations for further successful cooperation were laid. The project partners agree that the successful developments in the project will be exploited in the follow-up.
The compounding plant available at the Fraunhofer PAZ is available to interested users for trials and the production of material samples.