Weniger Prozessabbrüche und Baufehler durch halbautomatisierte Qualitätssicherung für 3D-gedruckte Bauteile
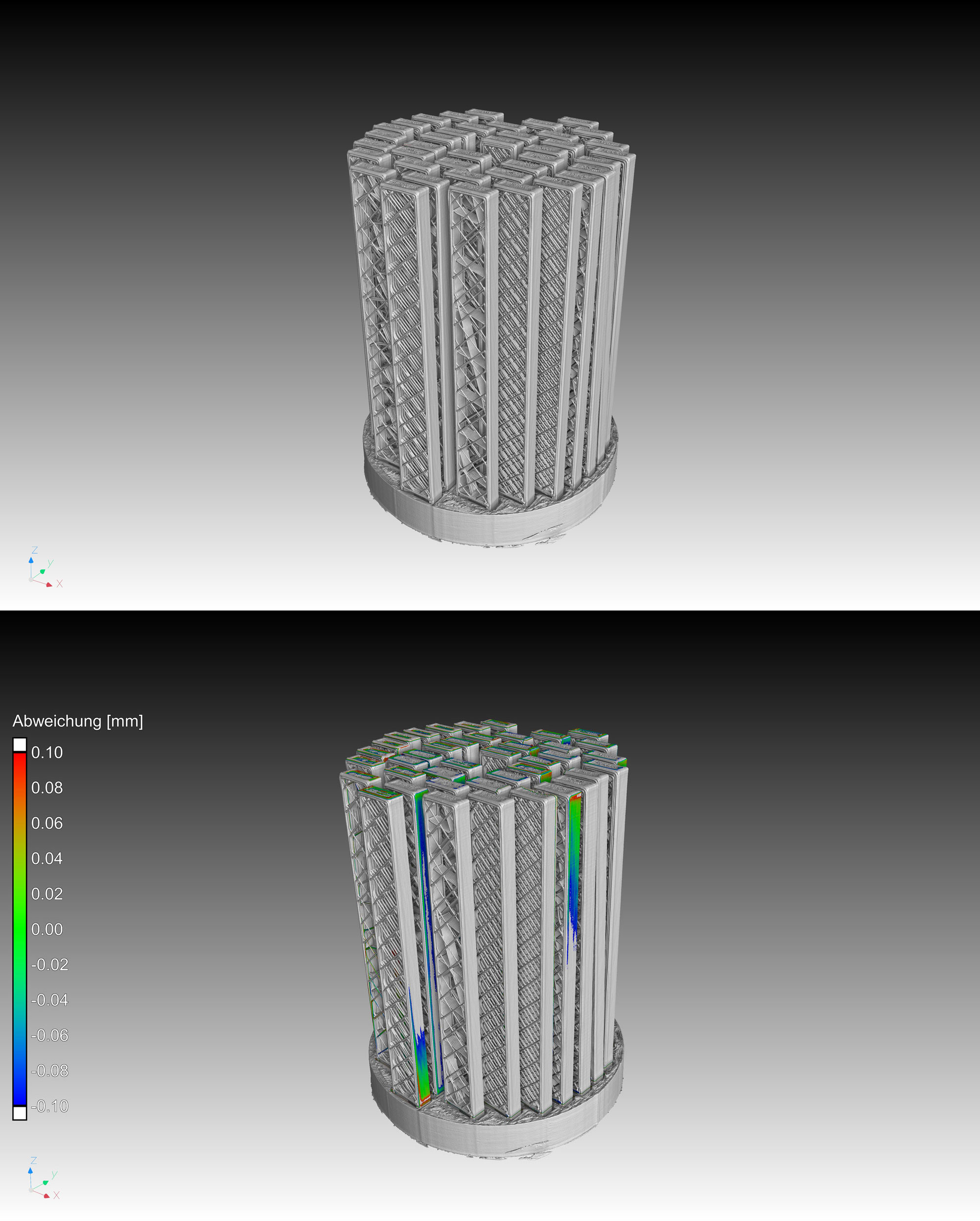

Die Digitalisierung von Produktionsprozessen ermöglicht enorme Effizienzsteigerungen in der industriellen Produktion. Eine Schlüsseltechnologie hierfür stellt die additive Fertigung dar. Dieses Verfahren ermöglicht es vom individualisiertem Einzelbauteil bis zur Fertigung von Kleinserien bis ca. 1000 Stück, Bauteile effizient und nachhaltig herzustellen. Vom Entwurf bis zur Fertigung ist der Arbeitsprozess digital.
Damit dieser Prozess im Sinne der Industrie 4.0 reibungslos funktionieren kann, müssen einzelne Schritte des Workflows jedoch angepasst werden. Die automatisierte Zuführung von Betriebs- und Rohstoffen, das Bauteiltracking, das Bauteilhandling und die automatisierte, auch stichprobenhafte Prüfung, stellen gegenwärtig jedoch eine noch zu lösende Herausforderung dar. Insbesondere die Anforderungen an eine automatische Qualitätssicherung spielen eine nicht zu unterschätzende Rolle.
Das Gemeinschaftsprojekt von Studio.201 Software GmbH und dem Fraunhofer IMWS konzentriert sich auf die halbautomatisierte Qualitätssicherung für 3-D gedruckte Bauteile. Die zentrale Idee des Ansatzes ist, dass eine Vielzahl additiv gefertigter Bauteile parallel automatisch geprüft werden, um Bauteilverzüge zu reduzieren und Fehlstellen aufzudecken. Dafür sollen Prozess- und Geometriedaten (Soll-Daten) mit ermittelten Messdaten aus der Computertomografie (Ist-Daten) an großen Stichproben (<100) verknüpft werden. Die durch diesen Prozess gewonnen Daten schaffen wiederum eine Datenbasis für das maschinelle Lernen, das in den nachfolgenden Prozessen benötigt wird. Ergänzt durch ein automatisiertes Bauteiltracking wird damit die Möglichkeit geschaffen, perspektivisch eine integrierte Prozesssteuerung aufzubauen. „Somit ist es möglich, automatisch Daten aus der Konstruktion und Vorentwicklung, begleitend durch Prozessdaten zu den Messdaten am Endbauteil in Zusammenhang zu setzen, um Anpassungen an der Technologie, Werkstoffauswahl oder in Schritte zur Nachbearbeitung umzusetzen, womit sich die Reproduzierbarkeit verbessert,“ so Andreas Krombholz, Leiter des Projektes am Fraunhofer IMWS.
Aufgrund der höheren Vielfalt von Variationen in der additiven als in der herkömmlichen Fertigung werden die Variationen im vorliegenden Verfahren im Rahmen einer automatisierten Bewertung mittels Massive Parallel Testing (MPT) geprüft. Ausgehend von der Entwurfsgeometrie eines Bauteils wird automatisch eine Vielzahl von konstruktiven Versionen erstellt, diese mit den Varianten des Herstellungsprozesses und unterschiedlichen Werkstoffen kombiniert und additiv gefertigt. Hierzu wird eine Tracking- und Handlingsystem entwickelt, um die gedruckten Bauteile für die Strukturuntersuchung mittels Computertomographie vorzubereiten und dann mikrostruktur-technisch zu untersuchen. Begleitet und dokumentiert wird dies durch ein Datenmanagementsystem. Zum Abschluss liegt zu jeder gefertigten Variante eine quantitative Bewertung sowie eine Aussage in Form eines Ampelsystems vor. Dies ermöglicht es dem Anwender optimale Baueil-Werkstoff-Prozessvarianten zu erkennen und dann diese optimierten Bauteile in Kleinserien zu fertigen.