The electronic control unit for a car engine or the power inverter in a wind turbine must perform heavy work. Such components are therefore integrated into protective casings, which are often made of plastics. The casings are then exposed to rough outside environments instead of the sensitive electronics: They are stressed by humidity, heat and strong electromagnetic fields. In a joint project with 3P GmbH, Fraunhofer IMWS researchers are exploring how such plastic casings behave under these conditions in the electric field and how materials could be made, which are best suited for electronic components.
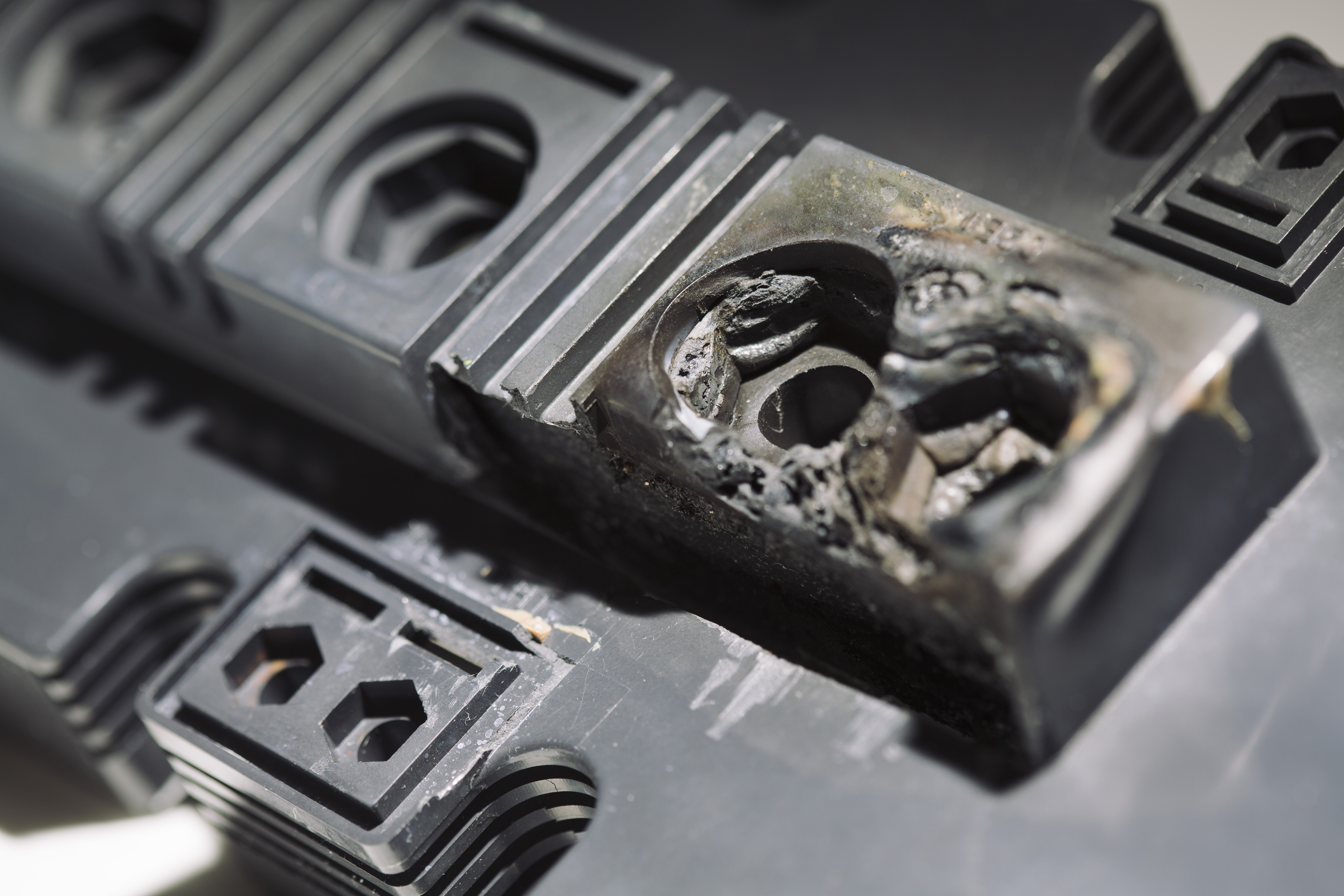

Ultimately, the reliability of electronics depends on the reliability of the casings: components may fail when dampness suddenly enters or the casing becomes a conductor of electricity – the wind turbine stops or the car’s engine no longer works properly. The optimal casing material should therefore have certain properties, for example low damp penetration, high resistance against chemicals, high mechanical and thermal stability.
During the course of the project »Design4LES«, which runs until June 2018, Fraunhofer IMWS and Präzisions-Plastic-Produkte GmbH (3P GmbH) in Neu-Staßfurt want to characterise conventional casing materials as to their behaviour in the electric field. For this specialised test, pieces are to be designed for electric tests and manufactured in injection moulding processes.
This makes it possible for the first time to research failure processes and mechanisms under direct impact of dampness. What happens precisely when the material is put under stress? How do defects occur when the material is exposed to extreme damp? What impact might this have on adjoining electronic components? The project partners explore these questions and hereby examine the glass fibre strengthened plastics down to microstructural level.
»So far there has been no sound scientific understanding amongst experts of these processes. The connection between microstructure, the pores or the binding of the glass fibres in plastics, the processing technologies and the electric failure behaviour of thermoplastic materials, when under the influence of damp, is largely unknown«, says Sandy Klengel, who leads the project at Fraunhofer IMWS. »We are therefore placing particular emphasis on the mechanisms, which result in restricting performance when damp enters thermoplastic casing materials. We are examining how the structure of materials changes and what impact this has on the properties of the material. Above all, this is a critical question for applications in performance electronics.«
Evaluation, modelling and diagnostic processes are to be developed as a second step after the test samples have been established. Material formulation as well as the processing steps in manufacture can thus be optimised – such as the appropriate values for temperature, retention times and injection moulding parameters like injection and holding pressure. This may result in innovative thermoplastic casing materials and improved manufacturing technologies, significantly increasing the quality and performance of casings for electronics.