Electronic components for automotive applications are exposed to complex stress conditions, which in turn poses significant challenges to quality control processes. The Fraunhofer IMWS has described the causes of corrosion defects in dielectric layers of a Hall sensor under the influence of various stress factors. It was then possible to verify a new kind of corrosion mechanism at the chip level.
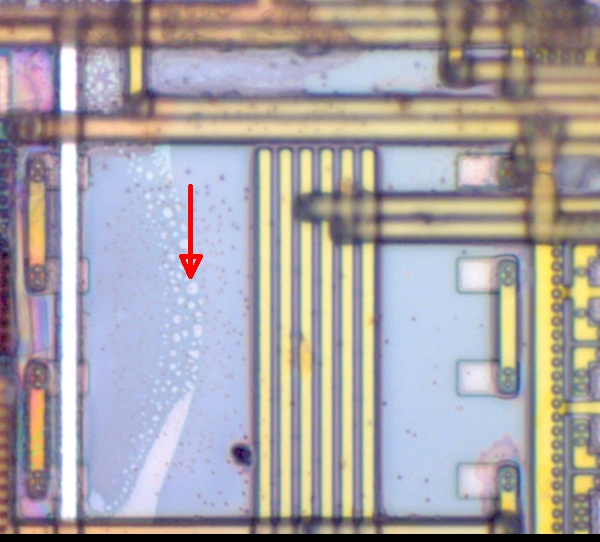
Hall sensors are used in cars for numerous magnetic switching tasks. The sensors are therefore exposed to different stress situations depending on their design and how they are used. When in direct contact with the environment, they are exposed to high stresses due to moisture and temperature changes with the corresponding thermomechanical stress on the components. The sensors are also exposed to mechanical stresses due to the component packaging, for example overmolding, as well as process- and application-related contamination in connection with moisture that affects the sensors.
In one study the Fraunhofer IMWS used its extensive knowledge in reliability analysis to analyze the causes of failure in the field of Hall sensors used for headlight range control and throttle control. This type of sensor was designed with special protective structures on the edge of the chip to prevent cracking on the sawed edge of the wafer from spreading into the electrically active structure of the circuit. Upon opening, all sensors of the components exhibited massive corrosion at similar locations on the silicon substrate and insulating layers of the semiconductor. The cause of the electrical failure of the components is that this corrosion progressed until it reached the vertical plated through-holes of the metal layers. This process is very slow and can take up to several months, and in some cases even years, which means vehicles only failed after several tens of thousands of kilometers.
Using high-resolution diagnostics with electron microscopy as well as time-of-flight secondary ion mass spectrometry and accompanying thermomechanical simulation, it was possible to fully clarify the failure mode. On locally prepared cross-sections in the area of the defect, a series of three successive corrosion processes were discovered that start on the edge of the chip and progress into the active circuit structures. In the first step, the silicon on the edge of the chip in the trench, which is not locally passivated, is converted chemically near the surface into a gel-like silica with an orientation-independent etching rate. After that, the dielectric insulator between the metal layers degraded, including the formation of cavities, and also converted to silica. In the third step, the plated through-holes nearby corroded chemically/electrochemically until they were electrically discontinuous, causing the electrical failure of the Hall sensor.
The chemical reactions are triggered by verified potassium contamination and the penetration of moisture. Since this type of corrosion was only observed in individual applications of the Hall sensors and only occurred on certain edges of the chips, additional external mechanical stress factors acting on the component were examined as potential triggers of the corrosion process. A finite element simulation (FEM) of the overmolded chip showed that the component was subject to thermomechanical stress due to the packaging process. It was shown that the area of the beveled molded edge of the housing was subject to increased hydrostatic tensile stress, which facilitates the diffusion of water in combination with ionic contamination from outside.
At the same time, a locally higher hydrostatic tensile stress acting on the surface of the chip was found near the corroded area. In combination with moisture, this promotes the penetration of corrosive media (for example potassium hydroxide) at the chip level as well, thus enabling corrosion of the active circuit structures. Since the failure mechanism only occurs on certain components, each with different installation situations, the effect of a targeted external mechanical stress was also simulated thermomechanically. This simulation showed that when subject to a positive bending moment – which occurs in applications due to the additional plastic overmolding – the hydrostatic stresses in the silicon near the surface increased further and eventually triggered the chemical corrosion actually observed.
To test the failure hypothesis, a reproduction experiment was set up in which the Hall sensor was exposed to a damp potassium hydroxide atmosphere. During the test, some of the sensors were operated electrically while others were also subjected to an additional mechanical load by an external clamping device. The results showed that only the Hall sensors subjected to the additional mechanical stress exhibited corrosion on the corresponding edges of the chips. In summary, it was possible to verify a new kind of corrosion mechanism at the chip level. This mechanism is triggered by the penetration of moisture and contaminants and is facilitated by the geometry of the plastic overmolding, the internal thermomechanical stresses in the housing, and an external mechanical load from the overmolding or the installation of the component.