Fraunhofer IMWS und Partner entwickeln Kindersitz aus biobasierten Materialien
Faser-Kunststoff-Verbunde auf Basis von Biopolymermatrix und kontinuierlicher Naturfaserverstärkung (Bio-NFK) sollen zukünftig auch für Leichtbaustrukturen eingesetzt werden – also Bauteile, die bei geringerem Gewicht höchste Last aushalten und Stabilität gewährleisten. Am Beispiel einer Kindersitz-Demonstratorstruktur fürs Auto demonstriert das Fraunhofer-Institut für Mikrostruktur von Werkstoffen und Systemen IMWS gemeinsam mit den Projektpartnern Evonik Nutrition & Care GmbH, SachsenLeinen GmbH, Technische Universität Chemnitz und EDAG Engineering GmbH, sowie GK Concept GmbH, Britax Römer Kindersicherheit GmbH, Knoten Weimar GmbH und ID Berlin, welche Möglichkeiten die neu zu entwickelnden Material-, Technologie- und Bauteildesignkonzepte für naturfaserverstärkte Biopolymere bieten.
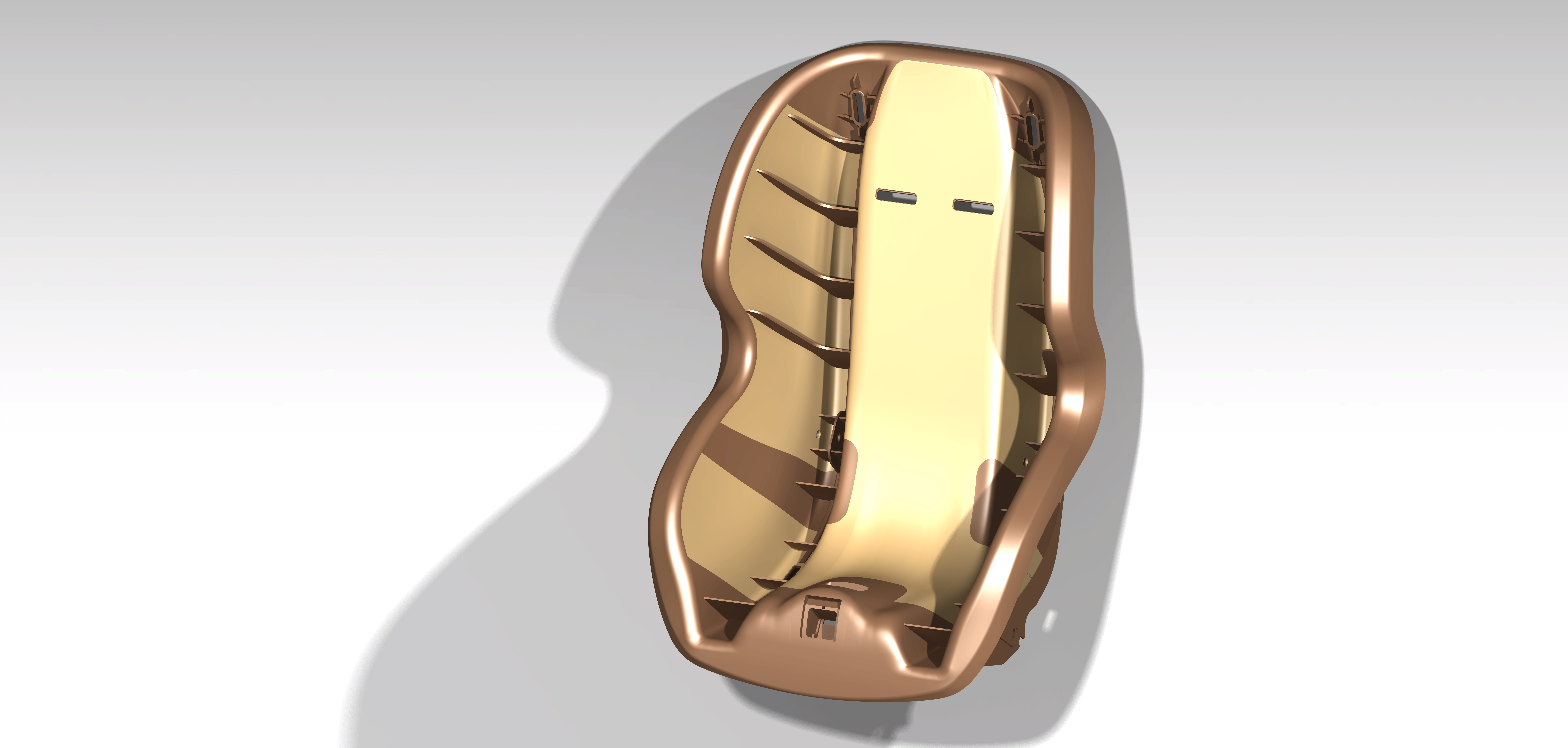
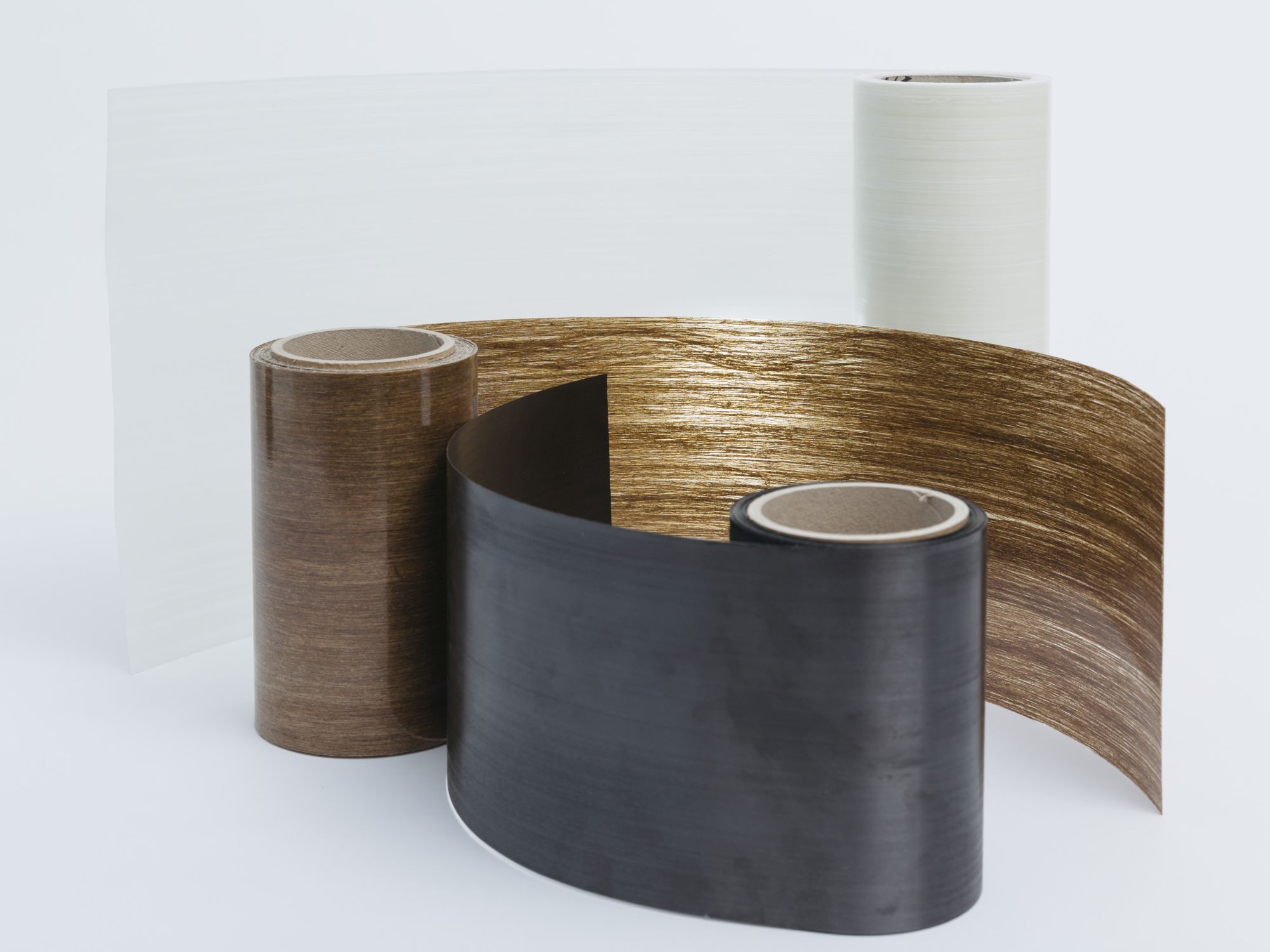
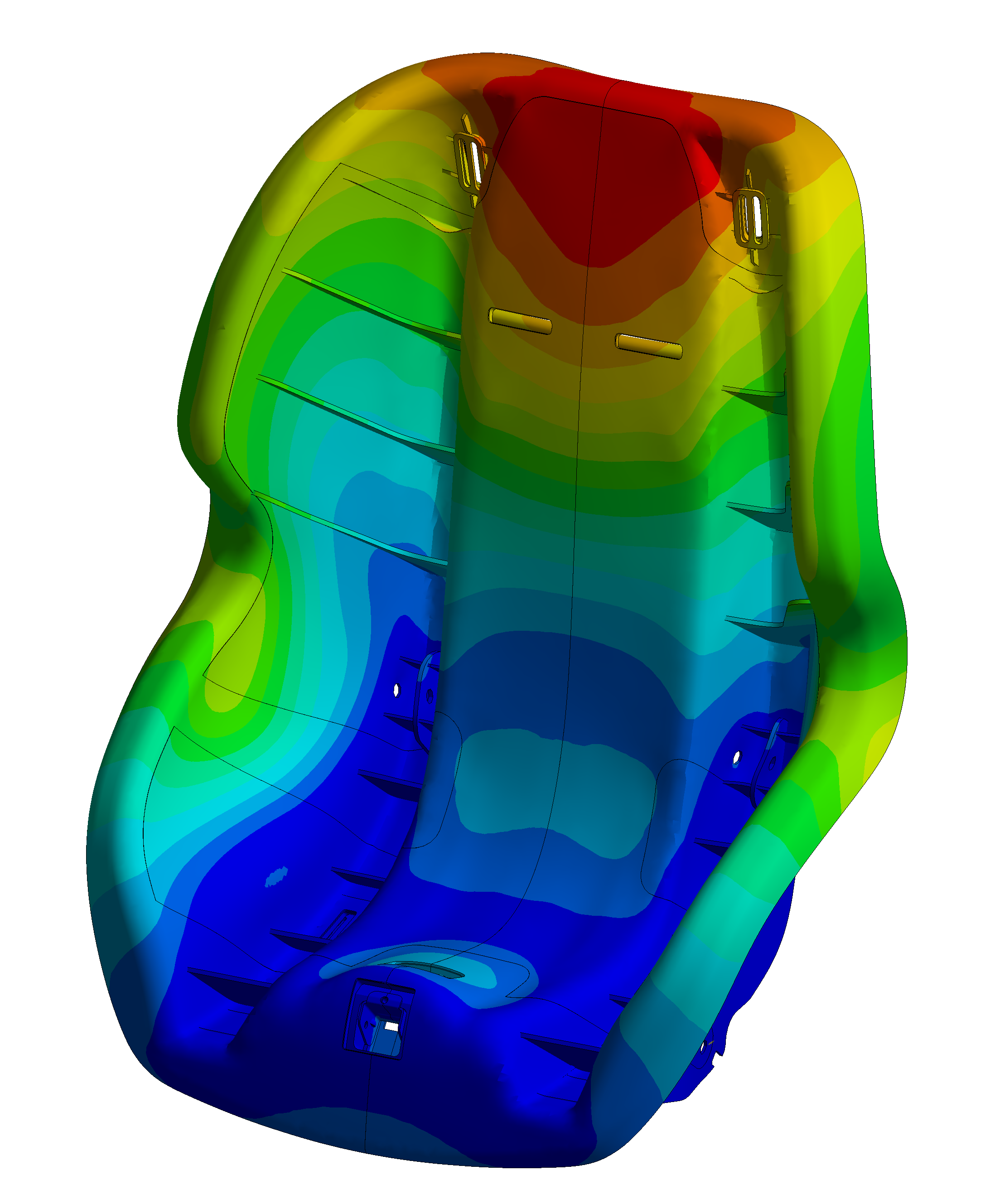
Leichtbauprodukte aus der Flugzeug- und Automobilindustrie bestehen häufig aus herkömmlichen Kunststoffen auf Basis von Erdöl und anorganischen Fasern (z.B. Carbon- oder Glasfaser). Sie leisten bereits einen erheblichen Beitrag zum Umweltschutz, denn leichtere Luft- und Straßenfahrzeuge verbrauchen weniger Treibstoff. Noch nachhaltiger werden solche Lösungen, wenn die Polymermatrix selbst aus biobasierten Ausgangsstoffen besteht und für die Verstärkungsfasern beispielsweise einheimische pflanzliche Fasern eingesetzt werden.
Dass diese biobasierten Werkstoffe auch für Hochleistungs-Anwendungen eingesetzt werden können, soll in dem Verbundprojekt, das vom Bundesministerium für Ernährung und Landwirtschaft gefördert wird, gezeigt werden. Dabei sollen thermoplast- und duroplastspezifische Werkstoffeigenschaften in einem Hybridbauteil so kombiniert werden, dass sie hohen Struktur- und Sicherheitsanforderungen gerecht werden. Im Rahmen des Projekts ist die Erforschung der Material-, Technologie- und Auslegungskonzepte für Bauteilanwendungen auf Basis naturfaserverstärkter Biopolymere zunächst im Labormaßstab und im Anschluss eine Übertragung in den Pilotmaßstab vorgesehen. Im Ergebnis sollen diese neu entwickelten Materialien, Technologien und Bauweisen anhand eines hybridspritzgegossenen Demonstrators in Form einer Kindersitzschale validiert werden.
Um dies zu realisieren, werden gemeinsam mit den Projektpartnern verschiedene Arbeitspakete bearbeitet. Das erste wichtige Teilziel konzentriert sich auf die Erforschung und Weiterentwicklung von modifizierten biobasierten Thermoplast-Materialien, die mit Naturfasern zum Spritzgusscompound sowie zum endlosfaserverstärkten Hochleistungsverbund kombiniert werden und spezielle Eigenschaften aufweisen müssen. »Wir wollen uns auf die Verwendung von einheimischen Naturfasern wie Bastfasern oder Cellulose als Verstärkungsmaterial konzentrieren und das Eigenschaftsprofil der Polymermatrix so anpassen, dass sie für Hochleistungsverbunde geeignet und darüber hinaus sehr gut zu verarbeiten sind«, sagt Ivonne Jahn, Teilprojektleiterin »Bio-NFK-Halbzeuge« am Fraunhofer IMWS. Damit das gelingt, werden die Polymere mittels Elektronenbestrahlung nach der thermoplastischen Verarbeitung so modifiziert, dass sie durch die nachträgliche Vernetzung einen duroplastischen Charakter und somit verbesserte Eigenschaften für die mechanische Belastbarkeit und Wärmeformbeständigkeit aufweisen.
Das zweite wesentliche Teilziel konzentriert sich auf die Herstellung biobasierter quasi-endlosfaserverstärkter Halbzeuge. Als maßgeschneiderte Verstärkungseinleger für die anvisierten hybriden Hochleistungs-Produkte sollen im Bauteil belastungsgerechte und materialeffiziente Laminataufbauten aus unidirektionalen Einzelschichten, sogenannten Bio-UD-Tapes, fungieren. Die erzeugten UD-Tape-Halbzeuge werden zu einem Laminat verarbeitet; dabei können die Faserorientierungen des Halbzeugs an die spätere Belastung des Bauteils angepasst und die Preforms endkonturnah mit geringem Verschnitt aufgebaut werden.
Das dritte wichtige Teilziel beschäftigt sich mit der Auslegung und Herstellung von sicherheitsrelevanten Hybrid-Spritzgussbauteilen am Beispiel eines prototypischen Demonstrators in Form einer Sitzschale. Um darüber hinaus Aussagen über die Wiederverwertung treffen zu können, werden außerdem auch Recyclingkonzepte für biobasierte Leichtbaustrukturen erforscht. Somit sollen die entwickelten Material-, Technologie-, Recycling- und Auslegungskonzepte sowie die Überführbarkeit in die industrielle Fertigung von Leichtbauanwendungen validiert werden. »Wir können anhand des im Hybrid-Spritzgussprozess hergestellten Biopolymer-Demonstrators fundierte Aussagen über die Struktureigenschaftsbeziehungen und Belastungsgrenzen von Bio-NFK-Bauteilen treffen. Wenn sich alle Ziele erfolgreich umsetzen lassen, können wir insgesamt durch das erhöhte Leichtbaupotenzial und die thermoplastbasierte Leichtbauweise eine signifikante Gewichtsreduzierung sowie wirtschaftliche und nachhaltige Fertigung erreichen. Das heißt, wir entwickeln nachhaltigere Halbzeuge, die alle Anforderungen hinsichtlich der späteren Bauteilsicherheit erfüllen, und schonen somit unsere Umwelt«, erklärt Dr. Matthias Zscheyge, Teilprojektleiter »Bio-NFK-Hybridformteile« am Fraunhofer IMWS.