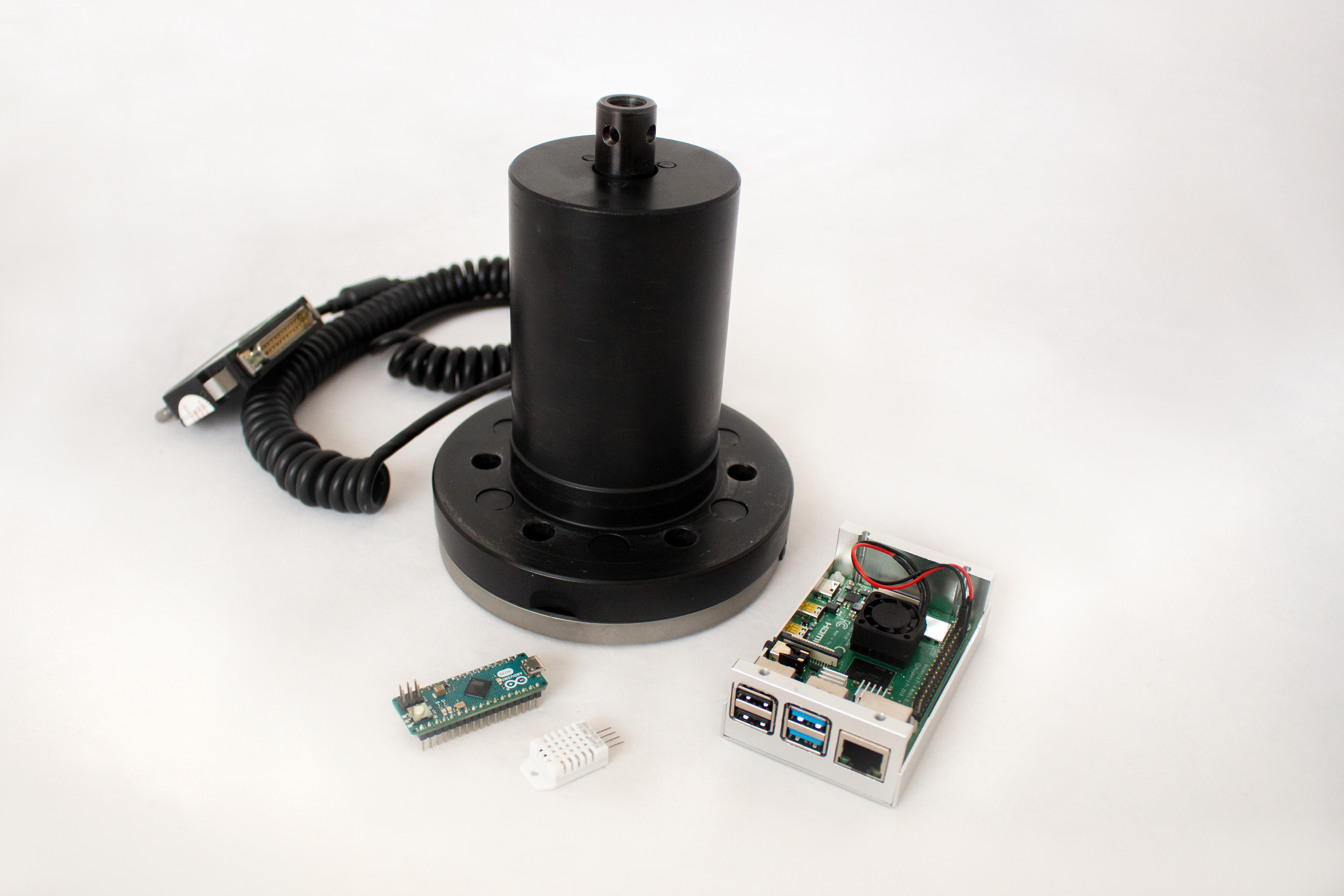
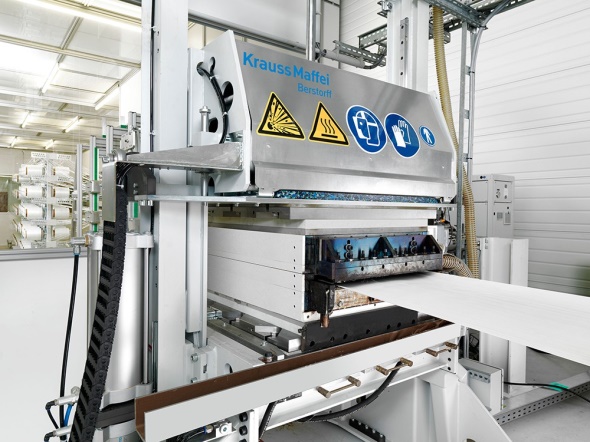

Smarte Prüftechnik kann die Datenbasis von digitalen Werkstoff-Zwillingen bereichern und so erhebliche Vorteile für die Industrie 4.0 generieren. Den Nachweis dafür wollen die studio.201 software GmbH und das Fraunhofer-Institut für Mikrostruktur von Werkstoffen und Systemen IMWS in einem nun gestarteten Gemeinschaftsprojekt am Beispiel einer digitalisierten Prozess- und Wertschöpfungskette in der Kunststoffverarbeitung erbringen.
Jedes Produkt hat eine Geschichte. Bis es den Kunden erreicht, hat es diverse Herstellungsschritte durchlaufen. Wie wäre es, wenn beispielsweise ein Kugelschreiber diese Geschichte erzählen könnte? Aus welchen Materialien besteht er, wo kommen diese her? Wer hat sie geliefert, wer hat sie wie weiterverarbeitet? Und wie haben sich beispielsweise Temperatur und Druck in einem Spritzgussprozess konkret auf das Material in diesem Kugelschreiber ausgewirkt?
Solche Fragen kann der digitale Zwilling beantworten, der Bauteil- und Werkstoffdaten über den gesamten Lebenszyklus hinweg speichert. Durch das Sammeln, Verknüpfen und Auswerten dieser Daten lassen sich enorme Effizienzgewinne erzielen. In einem neuen Gemeinschaftsprojekt wollen die studio.201 software GmbH aus Magdeburg und das Fraunhofer IMWS dafür Lösungen entwickeln, um die Leistungsfähigkeit des Konzepts am Beispiel der Kunststoffverarbeitung zu demonstrieren.
»Die Digitalisierung der industriellen Produktion ist in vollem Gange, beispielsweise bei der Verschleißerfassung von Maschinen oder Verbesserungen in der Logistikkette. Für die explizite Betrachtung der eingesetzten Werkstoffe und Halbzeuge wird der digitale Zwilling aber praktisch noch gar nicht genutzt. Dabei bieten sich gerade hier erhebliche Vorteile. Denn kleinste Schwankungen bei der Fertigung können erheblichen Einfluss auf die Bauteilqualität haben«, sagt Alexander Goldstein, der das bis Ende Februar 2022 laufende Projekt am Fraunhofer IMWS leitet.
Erste Voraussetzung dafür ist eine möglichst korrekte und effiziente Erfassung der Materialzustände und -veränderungen. Solche Daten werden bereits heute mit Sensoren erfasst. Doch entlang der komplexen Wertschöpfungskette sind sehr viele verschiedene Sensoren im Einsatz, die sehr unterschiedliche Messdaten erfassen, teils in verschiedenen Formaten. Ziel des Forschungsprojekts ist es, diesen Prozess zu vereinfachen und zugleich die an den verschiedenen Punkten der Wertschöpfungskette entstehenden Daten besser zu verknüpfen. Ein smartes Sensorsystem soll die Materialeigenschaften vollständig und zusammenhängend erfassen und dabei auch das Einsatzleben der Sensoren selbst berücksichtigen. So wird einfacher erkennbar, welches Zusammenspiel zwischen Material und Prozess das bestmögliche Produkt hervorbringt. Ein weiterer Vorteil des intelligenten Sensorsystems, das zum Projektabschluss als Prototyp vorliegen soll: Die Kontrolle der mechanischen Materialeigenschaften erfolgt zum Teil direkt in der Fertigung. Es müssen nicht mehr, wie bisher, Stichproben aus der laufenden Produktion entnommen und dann aufwendig untersucht werden.
Das Beispiel, an dem die Forschungspartner die Verbesserungsmöglichkeiten demonstrieren wollen, ist ein Kraftsensor. Solche Sensoren machen geringe elastische Verformungen als elektrisch messbares Signal quantifizierbar und werden beispielsweise in der Materialprüfung eingesetzt. Im Projekt werden zunächst klassische Kraftsensoren zur mechanischen Charakterisierung analysiert, daraus wird dann ein Anforderungsprofil für ein smartes Sensorsystem abgeleitet. Dieses intelligente Sensorsystem werden die Projektpartner dann aufbauen und entlang einer Herstellungskette von thermoplastischen Faserverbundstrukturen (UD-Laminate aus UD-Tape Einzellagen) erproben.
Die nächste Herausforderung nach dem Messen der Daten ist die Schaffung eines geeigneten Datenraums, in den die Sensoren ihre Messergebnisse einspeisen können. Die Fraunhofer-Gesellschaft hat dafür die Plattform Materials Data Space initiiert, in der Materialdaten sicher, unternehmensübergreifend und entlang der gesamten Wertschöpfungskette bereitgestellt und verarbeitet werden können. Im Projekt werden dessen Anwendungsmöglichkeiten auf das Beispiel des mechanischen Verhaltens von thermoplastischen Faserverbundstrukturen heruntergebrochen: Welche Daten müssen enthalten sein, um eine komplette Wertschöpfungskette in der Kunststoffverarbeitung abzubilden? Wie sollen diese Daten strukturiert sein? Welche Materialeigenschaften sind in der großen Menge der Daten besonders relevant, welche weniger? Wie kann der Austausch vielfältigster Datenformate gelingen? Als Antwort darauf entwickeln die Projektpartner ein passendes Informationsmodell und eine Ontologie für die Herstellung und Bewertung von modernen Kunststoffbauteilen.
»Dieses Modell spiegelt die natürliche Werkstoffwelt. Wir wollen damit auch zeigen, was durch valide, reproduzierbare, gut strukturierte und sicher verfügbare Daten alles möglich ist. Die heute verfügbaren Materialdaten liegen oft isoliert an sehr unterschiedlichen Orten. Durch die Verknüpfung zu größeren Beständen wie im Materials Data Space eröffnen sich neue Möglichkeiten, um daraus wertvolle Schlüsse zu ziehen«, sagt Goldstein.
Die Idee der Vernetzung ist zentral für das neue Projekt. Zudem ist eine Übertragung des Konzepts auf andere Anwendungsbereiche jenseits der Materialcharakterisierung in der Kunststoffverarbeitung möglich. Goldstein: »Den Smartsensor verstehen wir als eine universell einsetzbare Komponente, die sowohl geräte- als auch herstellerübergreifend funktioniert. So können zum Beispiel Produktionssysteme digital vernetzt, flexibilisiert und im laufenden Betrieb werkstoffgerecht verbessert werden.«