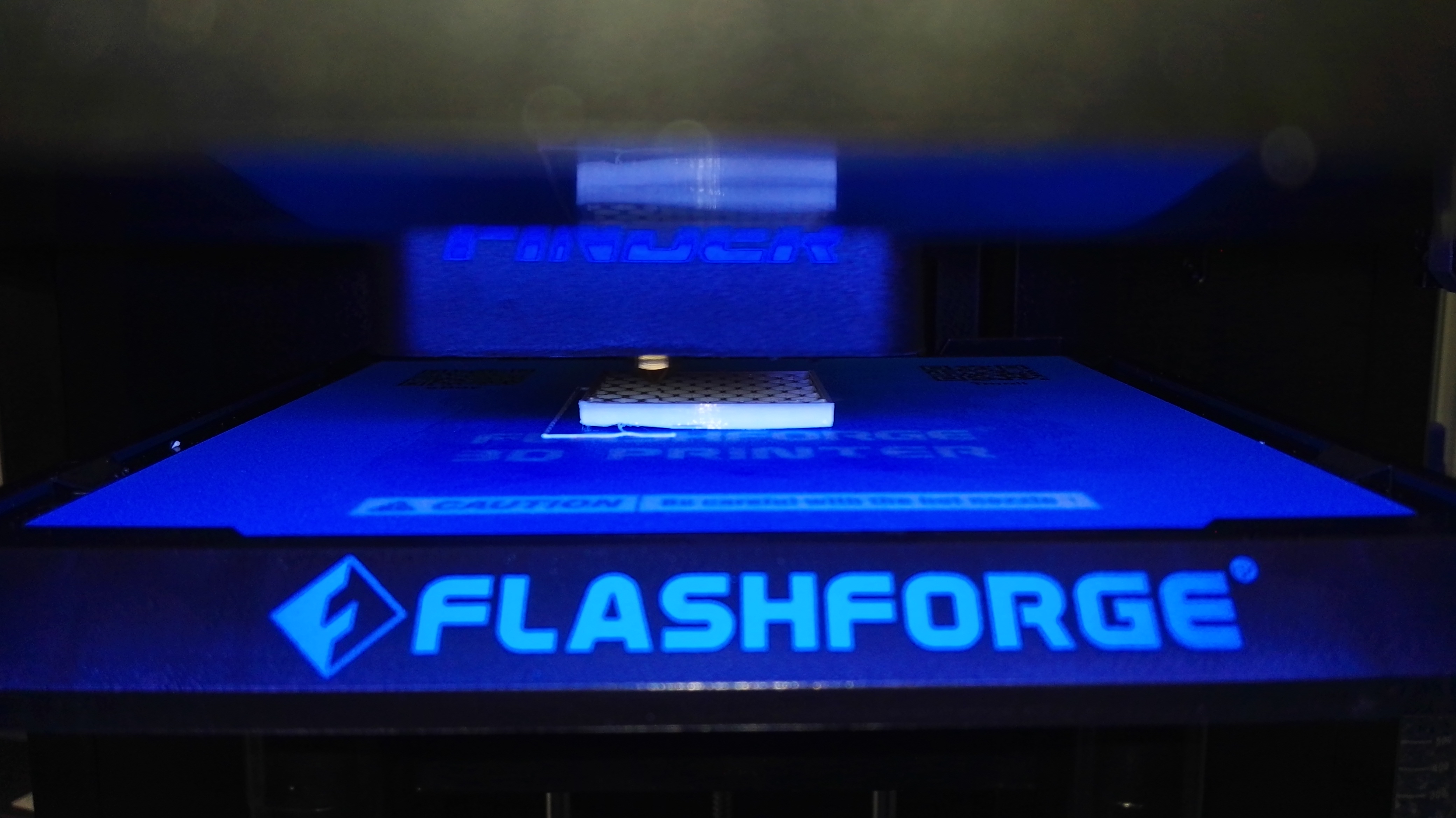

Mit elektrochemisch aktiven Polymerfüllkörpern, die in 3D-Druck-Verfahren hergestellt werden, wollen das Fraunhofer-Institut für Mikrostruktur von Werkstoffen und Systemen IMWS und die 3P Präzisions Plastic Produkte GmbH aus Staßfurt neue Lösungen für die Verfahrenstechnik, beispielsweise bei der Wasseraufbereitung, entwickeln. Sie setzen auf einen Kunststoff, der Strom leiten kann und somit den Bewuchs der Füllkörper mit Mikroorganismen verhindert.
Um Stoffgemische voneinander zu trennen, werden verschiedene technische Verfahren eingesetzt. Der Stoffaustausch kann beispielsweise mit einer Membran zwischen Bereichen mit höherer und niedrigerer Konzentration erfolgen oder durch thermische Trennverfahren, bei denen ein Gleichgewicht zwischen verschiedenen Phasen, etwa Gas- und Flüssigphase, hergestellt wird.
»Diese Verfahren haben eine hohe industrielle Bedeutung und werden etwa zum Entfernen von Verunreinigungen in Rohstoffen genutzt. Bekannte Verfahren sind Absorption oder Destillation. Die Einsatzfelder reichen von der Petrochemie bis zur Herstellung von Spirituosen. Eine besonders wichtige Anwendung ist die Wasseraufbereitung«, sagt Andreas Krombholz, Projektleiter am Fraunhofer IMWS.
Als verfahrenstechnische Apparate zur Stofftrennung werden häufig hohe, zylindrische Behälter eingesetzt, sogenannte Kolonnen. Sie sind so gestaltet, dass die Trennung der Gemische darin ideal funktioniert. Bei bestimmten Verfahren enthalten die Kolonnen zusätzliche Füllkörper aus Glas, Keramik, Metall oder Kunststoffen. Sie sind meist nur wenige Zentimeter groß, verbessern aber durch ihre spezielle Form den Trennprozess zusätzlich, indem sie für eine gute Verteilung der Flüssigkeit und Verwirbelung der Gasströmung innerhalb der Kolonne sorgen.
Die Füllkörper sind während des Betriebs der Anlagen den sie umgebenden Medien ausgesetzt. Beispielsweise bei der Abwasserreinigung oder in Entsalzungsanlagen sind im Wasser auch Bakterien und Mikroorganismen wie Algen sowie einzellige Tiere und Pilze enthalten, die sich nach und nach an den Füllkörpern absetzen. Dieses »Biofouling« vermindert die Wirkung der Füllkörper und damit die Leistungsfähigkeit der Kolonnen, bis hin zum Prozessabbruch.
Im bis April 2022 laufenden Projekt wollen die Kooperationspartner für dieses Problem eine Lösung entwickeln. Sie setzen auf elektrochemisch aktive Füllkörper, die im 3D-Druck hergestellt werden. »Wenn die Füllkörper elektrochemisch aktiv sind, erfolgt kein Bewuchs durch Mikroorganismen, das Biofouling wird also verhindert. Der 3D-Druck bietet weitere Vorteile, beispielsweise eine hohe Gestaltungsfreiheit bei der Form der Füllkörper«, erklärt Krombholz.
Die Füllkörper sollen aus elektrisch leitfähigen Polymeren gefertigt werden, die in korrosiven Medien einsetzbar sind. Die Leitfähigkeit ist entscheidend, um das Biofouling ausreichend zu unterdrücken. Zunächst gilt es deshalb, ein entsprechendes Kunststoff-Compound zu entwickeln und daraus ein Filament zu erstellen, das als Ausgangsmaterial für den 3D-Druck genutzt werden kann. Als Druckmethode setzen die Projektpartner auf das etablierte Fused Deposition Modelling (FDM, auch bekannt als Schmelzschichtungsverfahren). Dabei wird der Kunststoff erhitzt und durch Düsen gepresst. Heraus kommt ein extrem feiner, zähflüssiger Faden, mit dem dann Schicht für Schicht das gewünschte Bauteil geformt wird.
Neben der Entwicklung von Compound und Filamenten gilt es im Projekt auch, Füllkörpergeometrien zu finden, die besonders für den Einsatz in Kolonnen geeignet sind. Nachdem die Füllkörper mit einem Lacksystem zur Erreichung eines elektrochemischen Antifouling-Effekts in wässrigen Medien beschichtet wurden, wird ihre Leistungsfähigkeit hinsichtlich Mechanik, elektrochemischem Verhalten, Strömungsverhalten und Medienbeständigkeit geprüft. Zudem möchten die Projektpartner den Prototyp eines Spritzgusswerkzeugs fertigen und die Prüfkörper in einer Kleinserie herstellen, um sie in einem Laborreaktor weiter analysieren zu können.
»Der Bedarf nach neuen und besonders leistungsfähigen Füllkörpern steigt, beispielsweise für eine sichere Wasserversorgung in Zeiten des Klimawandels. Mit dem Einsatz von additiven Fertigungsverfahren wollen wir vor allem die Entwicklungszeiten verkürzen. Durch den 3D-Druck können neue Formen und Materialien schneller getestet und für neue Kolonnen und moderne Verfahrenstechnik optimiert werden«, sagt Krombholz. Um diesen Prozess weiter zu beschleunigen, wird im Forschungsprojekt auch ein »digitaler Zwilling« der neu entwickelten Füllkörper entstehen. So wird es möglich, ihr späteres Einsatzverhalten durch Simulationen zu verkürzen und somit noch schneller passende Bauteile anbieten zu können.